Use VCE Exam Simulator to open VCE files
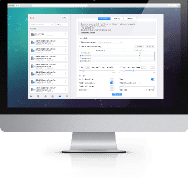
100% Latest & Updated ASQ CQE Practice Test Questions, Exam Dumps & Verified Answers!
30 Days Free Updates, Instant Download!
CQE Premium Bundle
ASQ CQE Practice Test Questions, ASQ CQE Exam Dumps
With Examsnap's complete exam preparation package covering the ASQ CQE Test Questions and answers, study guide, and video training course are included in the premium bundle. ASQ CQE Exam Dumps and Practice Test Questions come in the VCE format to provide you with an exam testing environment and boosts your confidence Read More.
ExamSnap's ASQ CQE Practice Test Questions and Exam Dumps, study guide, and video training course are complicated in premium bundle. The Exam Updated are monitored by Industry Leading IT Trainers with over 15 years of experience, ASQ CQE Exam Dumps and Practice Test Questions cover all the Exam Objectives to make sure you pass your exam easily.
Purchase Individually
CQE Training Course
SPECIAL OFFER: GET 10% OFF
This is ONE TIME OFFER
A confirmation link will be sent to this email address to verify your login. *We value your privacy. We will not rent or sell your email address.
Download Free Demo of VCE Exam Simulator
Experience Avanset VCE Exam Simulator for yourself.
Simply submit your e-mail address below to get started with our interactive software demo of your free trial.