Use VCE Exam Simulator to open VCE files
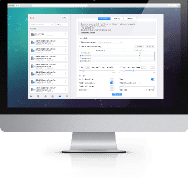
Get 100% Latest Lean Six Sigma Practice Tests Questions, Accurate & Verified Answers!
30 Days Free Updates, Instant Download!
Six Sigma Lean Six Sigma Certification Practice Test Questions, Six Sigma Lean Six Sigma Exam Dumps
ExamSnap provides Six Sigma Lean Six Sigma Certification Practice Test Questions and Answers, Video Training Course, Study Guide and 100% Latest Exam Dumps to help you Pass. The Six Sigma Lean Six Sigma Certification Exam Dumps & Practice Test Questions in the VCE format are verified by IT Trainers who have more than 15 year experience in their field. Additional materials include study guide and video training course designed by the ExamSnap experts. So if you want trusted Six Sigma Lean Six Sigma Exam Dumps & Practice Test Questions, then you have come to the right place Read More.
Study with ExamSnap to prepare for Six Sigma Lean Six Sigma Practice Test Questions and Answers, Study Guide, and a comprehensive Video Training Course. Powered by the popular VCE format, Six Sigma Lean Six Sigma Certification Exam Dumps compiled by the industry experts to make sure that you get verified answers. Our Product team ensures that our exams provide Six Sigma Lean Six Sigma Practice Test Questions & Exam Dumps that are up-to-date.
SPECIAL OFFER: GET 10% OFF
This is ONE TIME OFFER
A confirmation link will be sent to this email address to verify your login. *We value your privacy. We will not rent or sell your email address.
Download Free Demo of VCE Exam Simulator
Experience Avanset VCE Exam Simulator for yourself.
Simply submit your e-mail address below to get started with our interactive software demo of your free trial.