Use VCE Exam Simulator to open VCE files
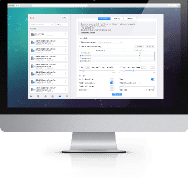
C_TS413_2021 SAP Practice Test Questions and Exam Dumps
Question 1
The technical completion of the current maintenance order was posted with a delay of 5 days. What happens to the next planned date if you set the shift factor for early completion to 100%?
A. It is postponed by a full cycle (100%).
B. It is postponed by 5 days.
C. It is not shifted.
D. It will be 5 days earlier.
Correct Answer: D
Explanation:
In SAP, the concept of shift factors is used to adjust the timing of maintenance activities based on the actual completion time of a maintenance order compared to the planned completion date. When a maintenance order is delayed or completed earlier than planned, the shift factor helps adjust the timing for the next scheduled maintenance activity.
Let’s analyze the scenario where the current maintenance order was delayed by 5 days, and the shift factor for early completion is set to 100%.
A shift factor for early completion indicates how much the next planned date should change when the current maintenance order is completed earlier than planned. A shift factor of 100% means that if the task was completed early, the next planned date would be shifted forward by the same amount of time as the early completion.
In this case, since the current maintenance order was delayed, the concept of early completion would lead to a shift in the opposite direction — the next planned date would be moved earlier.
A. It is postponed by a full cycle (100%).
This is incorrect. The shift factor of 100% refers to adjusting the next scheduled date based on how much earlier the task was completed, not a full cycle of delay or rescheduling.
B. It is postponed by 5 days.
This is incorrect. Since the current maintenance order was delayed by 5 days, it would not simply be postponed by another 5 days, as this does not align with the concept of the shift factor for early completion. The shift factor for early completion would adjust the next planned date to reflect a potentially earlier time, not a delay.
C. It is not shifted.
This is incorrect. The shift factor would still apply, even if the task was delayed. The delay impacts the next planned date, and the shift factor ensures the timing is adjusted accordingly.
D. It will be 5 days earlier.
This is correct. Since the maintenance order was delayed by 5 days, and the shift factor for early completion is set to 100%, the next planned date will be shifted 5 days earlier. This adjustment compensates for the delay by anticipating an earlier start for the next cycle, making up for the delay in the current cycle.
A shift factor of 100% for early completion ensures that the next planned date is adjusted based on the delay or early completion of the current maintenance task. Since the current maintenance order was delayed by 5 days, the next planned date will be 5 days earlier to compensate for the delay.
Question 2
What can be determined using the offset within a maintenance strategy?
A. The basic start date of the maintenance order
B. The call date for the maintenance order
C. The first due date of a maintenance package
D. The scheduled start date of the maintenance order
Correct Answer: C
Explanation:
In SAP Plant Maintenance (PM), maintenance strategies are used to plan and schedule maintenance activities in a systematic way. These strategies typically involve different types of maintenance packages and cycles to determine when maintenance tasks should be performed based on specific intervals (e.g., time-based or performance-based). The offset within the maintenance strategy plays a crucial role in determining the exact timing of the maintenance order and related activities. Let's analyze the options and how the offset affects each:
An offset is a time-based adjustment that is applied to a maintenance strategy to shift the due date of the maintenance task relative to a reference point (e.g., the start date, the first call, or the last maintenance activity). The offset helps fine-tune the timing of maintenance orders based on specific operational needs.
A. The basic start date of the maintenance order
This is incorrect. The basic start date of a maintenance order is typically determined based on the maintenance strategy and the work scheduling parameters, but it is not directly influenced by the offset. The offset is more concerned with the timing of the due date and the start date of specific tasks or cycles, not the initial start date.
B. The call date for the maintenance order
This is incorrect. The call date of a maintenance order refers to the date when a maintenance call is generated based on the strategy and maintenance plan. The offset does not determine the call date directly. Instead, the offset impacts the timing for subsequent due dates and execution points, after the call date has been determined.
C. The first due date of a maintenance package
This is correct. The offset within a maintenance strategy is used to determine the first due date of a maintenance package. In SAP PM, a maintenance package refers to a set of tasks that must be performed during a maintenance cycle, and the offset adjusts the timing of when these tasks should occur in relation to the maintenance intervals. By setting an offset, you can specify that the first due date for the maintenance package will be earlier or later than the original planned date, depending on the operational requirements.
D. The scheduled start date of the maintenance order
This is incorrect. The scheduled start date of a maintenance order is determined by the maintenance plan, including the maintenance strategy and the work scheduling settings, but it is not directly determined by the offset. The offset may impact when the maintenance order is due to be completed or when the tasks are expected, but the actual scheduled start date is usually fixed based on the overall maintenance planning logic.
The offset within a maintenance strategy primarily affects the first due date of a maintenance package by adjusting when the maintenance tasks should occur. It helps tailor the timing of maintenance work to better fit the needs of the organization or equipment.
Question 3
Which scheduling parameters are used in a multiple-counter plan? (Choose two.)
A. Scheduling period
B. Start date
C. Scheduling indicator
D. Factory calendar
Correct Answer: A, C
Explanation:
In SAP Plant Maintenance (PM), a multiple-counter plan is a type of maintenance plan that allows you to manage maintenance activities based on multiple counters or different measurement values, such as time-based (e.g., months, years) or performance-based (e.g., operating hours, kilometers). This plan type is particularly useful when the maintenance of equipment is based on various factors, and the counters track different types of data.
A. Scheduling period
This is correct. The scheduling period defines the interval of time between maintenance tasks. In a multiple-counter plan, the scheduling period is used to determine how often maintenance tasks should be performed based on the counters, which track the equipment's usage or time intervals. The scheduling period is one of the primary parameters that control when the next maintenance activity should be triggered, taking into account the different counters.
B. Start date
This is incorrect. While the start date is important for determining when a maintenance plan should begin, it is not specific to a multiple-counter plan. The start date sets the initial point from which maintenance tasks will be scheduled, but it does not directly define how the multiple counters will influence the scheduling. The start date is more of a general parameter that applies to all types of maintenance plans, not just multiple-counter plans.
C. Scheduling indicator
This is correct. The scheduling indicator is another crucial parameter used in a multiple-counter plan. It defines the method by which maintenance activities are scheduled, whether they are time-based, performance-based, or a combination of both. The scheduling indicator helps the system determine how the different counters (e.g., operating hours, cycles) should be considered for maintenance task scheduling. It plays a vital role in ensuring that maintenance is performed based on the specific needs of the equipment.
D. Factory calendar
This is incorrect. The factory calendar defines the working days and holidays for scheduling, but it does not directly influence the specific counter-based scheduling of maintenance tasks in a multiple-counter plan. While the factory calendar can be used to ensure that maintenance is not scheduled on non-working days, it is not one of the key parameters used for determining how multiple counters are tracked and how tasks are scheduled based on those counters.
A multiple-counter plan uses the scheduling period and scheduling indicator to determine when maintenance tasks are due, based on different counters (e.g., time, performance). These parameters ensure that maintenance is triggered at the appropriate intervals according to the various counters, allowing for flexible and accurate scheduling based on equipment usage or time intervals.
Question 4
How does a performance-based maintenance plan calculate the interval between start date and planned date?
A. Cycle length divided by annual performance
B. Cycle length divided by ((scheduling period) x (cycle modification factor))
C. Cycle length divided by monthly performance
D. Cycle length divided by (annual performance / 365)
Correct Answer: D
Explanation:
In SAP Plant Maintenance (PM), a performance-based maintenance plan calculates maintenance intervals based on the actual usage or performance of equipment, rather than a fixed time interval. The performance data is typically based on measuring counters such as operating hours, kilometers traveled, or production cycles. This type of plan is suitable for assets whose wear and tear are based on their actual performance rather than on a simple time-based schedule.
In a performance-based maintenance plan, the cycle length of maintenance (e.g., when the maintenance task should be performed) is determined by the actual performance data of the asset. The plan calculates the interval between the start date and the planned date by considering the performance data over time.
A. Cycle length divided by annual performance
This is incorrect. While annual performance is important in performance-based plans, this option doesn’t account for how the interval is distributed over time. The interval is not simply divided by the annual performance to calculate the planned date.
B. Cycle length divided by ((scheduling period) x (cycle modification factor))
This is incorrect. The scheduling period and cycle modification factor are involved in some scheduling scenarios, but this is not the standard method for calculating the interval in a performance-based plan. The interval calculation in performance-based plans relies on performance data (e.g., operating hours, kilometers) rather than these factors.
C. Cycle length divided by monthly performance
This is incorrect. The maintenance interval is not calculated directly from monthly performance data in this way. The monthly performance could be part of the data considered in calculating the maintenance date, but the actual method uses annual performance data for a more accurate annualized calculation.
D. Cycle length divided by (annual performance / 365)
This is correct. In a performance-based maintenance plan, the cycle length (the planned interval for maintenance) is calculated by dividing the annual performance by 365 (to get daily performance) and then using this value to calculate the interval. This calculation ensures that the maintenance schedule reflects the actual wear and tear on the equipment based on its performance over a period of time. Essentially, it adjusts the maintenance interval based on the equipment's daily performance, leading to an accurate and efficient scheduling of maintenance tasks.
A performance-based maintenance plan calculates the interval between the start date and the planned date by dividing the cycle length by the annual performance divided by 365. This method ensures the maintenance plan is based on actual usage or performance data, making it more relevant and accurate for equipment that operates based on performance rather than just time.
Question 5
The maintenance engineer creates a strategy plan with the call object maintenance order. Shift factors are set to 100%. Which date is relevant for the calculation of future planned dates if the maintenance work is delayed?
A. Planned end date of the maintenance order
B. Actual finish date of the maintenance order
C. Planned date of the next call, independent of maintenance order dates
D. Technical completion date of the maintenance order
Correct Answer: B
Explanation:
In SAP Plant Maintenance (PM), a strategy plan is used to schedule maintenance tasks for equipment based on a set of defined rules. A call object maintenance order refers to the maintenance order generated based on a maintenance plan. When the shift factors are set to 100%, it indicates that any delay or shift in the current maintenance order will be fully reflected in the calculation of future planned dates.
The key here is understanding how the system handles the delay in maintenance work and how it affects future maintenance planning.
A. Planned end date of the maintenance order
This is incorrect. The planned end date represents when the maintenance order is expected to be completed, but it is not the key date for calculating future maintenance dates when work is delayed. The planned end date is more focused on the current maintenance task, not the overall strategy or future calls.
B. Actual finish date of the maintenance order
This is correct. In a strategy plan, when the maintenance work is delayed, the actual finish date of the current maintenance order is the relevant date for calculating future planned dates. The actual finish date reflects when the work was actually completed, and based on this, the system will adjust future maintenance plans to align with the delay. Since shift factors are set to 100%, any delay in the completion of the maintenance order will fully impact the scheduled dates of subsequent tasks.
C. Planned date of the next call, independent of maintenance order dates
This is incorrect. The planned date of the next call is the planned date for the next maintenance task or call. However, this date does not account for any delays or changes to the maintenance order itself. The planned date for the next call is fixed, and future adjustments are based on the actual finish date, not an independent planned date.
D. Technical completion date of the maintenance order
This is incorrect. The technical completion date indicates when the maintenance order is technically completed (i.e., when all tasks have been done, and the system considers the order finished). However, this date may not always reflect when the maintenance work was actually completed. The actual finish date is the date when the maintenance work was completed, which is more relevant for recalculating future maintenance dates, especially in cases of delays.
When the maintenance work is delayed, and shift factors are set to 100%, the actual finish date of the maintenance order is the key date used to calculate the future planned dates. This ensures that the entire maintenance schedule adjusts in accordance with the actual completion of the current work, allowing the strategy plan to reflect accurate timing for subsequent tasks.
Question 6
Which of the following parameters are available when you define a new maintenance plan category? (Choose three.)
A. Completion date
B. Call object
C. Change documents
D. Order type
E. Maintenance activity type
Correct Answer: B, D, E
Explanation:
When you define a new maintenance plan category in SAP Plant Maintenance (PM), various parameters can be specified to control the behavior of the maintenance plan. These parameters help ensure that the maintenance plan is structured to meet the needs of the organization, and that the right processes and orders are created for the maintenance activities.
A. Completion date
This is incorrect. The completion date is not a parameter defined during the creation of a maintenance plan category. Instead, the completion date refers to the date when the maintenance work is finished and may be assigned to the maintenance order or task, but it is not a core parameter for creating a maintenance plan category.
B. Call object
This is correct. The call object refers to the object linked to the maintenance plan, such as the equipment, functional location, or a maintenance order. The call object defines what is being maintained and how the maintenance plan is applied. This is an important parameter when defining a new maintenance plan category, as it ensures the plan is associated with the right object for tracking and managing the maintenance tasks.
C. Change documents
This is incorrect. Change documents are related to tracking changes made to maintenance plans or other objects in SAP. They help keep a log of any changes, but this is not a parameter that is set when defining a maintenance plan category. It is more related to the tracking of modifications after the maintenance plan is created.
D. Order type
This is correct. The order type is an essential parameter when defining a maintenance plan category. It specifies the type of maintenance order that will be generated when the maintenance plan is executed, such as a corrective maintenance order, preventive maintenance order, etc. This helps in categorizing the type of maintenance and aligning it with the organization's maintenance processes.
E. Maintenance activity type
This is correct. The maintenance activity type is also defined when creating a maintenance plan category. It specifies the type of activity that is required for the maintenance task, such as inspection, repair, lubrication, etc. This helps define the scope of the work involved and ensures that the right activities are scheduled and performed.
When defining a new maintenance plan category, the parameters that are available include the call object, order type, and maintenance activity type. These parameters help to structure the maintenance plan and ensure that the right orders and activities are created based on the defined plan.
Question 7
You want to create a single-cycle plan with a cycle of 12 months. You use the scheduling indicator Time - key date. The orders should be called 3 months before the planned date. How can you set up the maintenance plan? (Choose two.)
A. Set the call horizon to 90 days.
B. Set the call horizon to 25%.
C. Set the call horizon to 75%.
D. Set the offset to 3 months.
Correct Answer: A, D
Explanation:
In SAP Plant Maintenance (PM), when setting up a single-cycle maintenance plan with a cycle of 12 months, the call horizon and offset are important parameters to control when maintenance orders should be created in advance of the planned maintenance date.
A. Set the call horizon to 90 days.
This is correct. The call horizon defines the time period before the planned maintenance date when the system will generate maintenance orders. Setting the call horizon to 90 days (which is equivalent to 3 months) ensures that the system will create orders 3 months before the planned maintenance date. Since the question specifies that orders should be called 3 months before the planned date, this is the correct setting for the call horizon.
B. Set the call horizon to 25%.
This is incorrect. The call horizon can be specified as either a number of days or a percentage. However, setting the call horizon to 25% would mean that the maintenance order would be created 25% of the total cycle time (which is 12 months). 25% of 12 months is 3 months, which could be a valid answer in theory. But typically, for this type of scenario, specifying the exact number of days (90 days) is more direct and clear than using a percentage.
C. Set the call horizon to 75%.
This is incorrect. Setting the call horizon to 75% would result in orders being created 75% into the cycle (which is 9 months after the start of the cycle). This does not match the requirement of calling orders 3 months before the planned date. Therefore, this option is not suitable.
D. Set the offset to 3 months.
This is correct. The offset determines the advance notice or shift for the maintenance plan. By setting the offset to 3 months, you ensure that the maintenance order is called exactly 3 months before the planned date, which aligns with the requirement of calling orders 3 months in advance of the planned maintenance.
To set up a maintenance plan that calls orders 3 months before the planned date with a 12-month cycle, you should:
Set the call horizon to 90 days (this specifies that orders will be generated 90 days before the planned date).
Set the offset to 3 months (this shifts the start of the maintenance plan to 3 months before the planned date).
Question 8
You want to set up a general maintenance task list for inspection rounds using the overall time confirmation as a simplified way to record measurement documents. What do you need to do? (Choose two.)
A. Assign a measuring point as a production resources/tools (PRT) to a task list operation.
B. Assign a piece of equipment with an allocated measuring point to a task list operation.
C. Assign an inspection document as a PRT to the task list operation.
D. Assign an inspection lot to the task list header.
Correct Answer: A, B
Explanation:
In SAP Plant Maintenance (PM), when creating a general maintenance task list for inspection rounds using the overall time confirmation as a simplified way to record measurement documents, you need to ensure the relevant measurement points and equipment are properly configured in the task list operations. Here's how to set it up:
A. Assign a measuring point as a production resources/tools (PRT) to a task list operation.
This is correct. A measuring point can be assigned as a Production Resources/Tools (PRT) to a task list operation. In this setup, the measuring point will be used to capture measurement data during the maintenance task. This is an effective way to record and track measurements for inspections during the maintenance task execution.
B. Assign a piece of equipment with an allocated measuring point to a task list operation.
This is correct. By assigning a piece of equipment with an allocated measuring point to a task list operation, you ensure that specific measurements will be taken for that equipment during the inspection rounds. The allocated measuring point is tied to the equipment, and it is used to record measurement readings for the inspection. This aligns with the objective of using the overall time confirmation to record measurements.
C. Assign an inspection document as a PRT to the task list operation.
This is incorrect. An inspection document would not typically be assigned as a PRT. Instead, the focus in this scenario is on using measuring points to capture measurement readings, not on using inspection documents as tools or resources in the task list operation. Inspection documents are generally used for different purposes in SAP, such as tracking inspection results but not directly linked to PRTs for capturing measurements.
D. Assign an inspection lot to the task list header.
This is incorrect. An inspection lot is used in quality management to track the results of inspections and is not directly linked to task list headers in maintenance. The main focus for this scenario is on measuring points tied to equipment in task list operations, not on using inspection lots for task list management.
To set up a general maintenance task list for inspection rounds and record measurement documents via the overall time confirmation, you need to:
Assign a measuring point as a PRT to the task list operation.
Assign a piece of equipment with an allocated measuring point to the task list operation.
These steps ensure that the necessary measurements can be recorded and tracked during the inspection rounds in the maintenance process.
Question 9
You create two maintenance packages and only one package should be executed at a time. Which parameter determines this?
A. Lead flow
B. Hierarchy
C. Cycle set sequence
D. Package sequence
Correct Answer: D
Explanation:
In SAP Plant Maintenance (PM), when managing multiple maintenance packages that need to be executed in a specific order (i.e., only one package should be executed at a time), the Package sequence parameter plays a crucial role. This setting ensures that the packages are processed in a predefined order, preventing them from overlapping or being executed simultaneously.
A. Lead flow
This is incorrect. The lead flow parameter relates to the sequence in which operations are processed within a maintenance order, but it does not specifically control the execution order of maintenance packages. Lead flow primarily affects the scheduling and timing within the maintenance order itself, rather than the relationship between separate maintenance packages.
B. Hierarchy
This is incorrect. The hierarchy in maintenance packages refers to the relationship between packages or tasks in terms of structure or dependencies. While the hierarchy may influence the logical relationships between tasks or packages, it does not directly control the execution order of maintenance packages.
C. Cycle set sequence
This is incorrect. The cycle set sequence refers to the order of cycles within a maintenance strategy and is related to the scheduling of cyclical maintenance tasks. It is not used to control the execution of individual maintenance packages. The cycle set sequence would be more relevant for determining the scheduling of maintenance tasks over time, rather than controlling which package is executed first.
D. Package sequence
This is correct. The package sequence is the parameter that determines the order in which multiple maintenance packages are executed. By defining the package sequence, you can ensure that only one package is executed at a time, based on the specified sequence. This is essential when there are dependencies or specific requirements that must be met before the next maintenance package is carried out.
To ensure that only one maintenance package is executed at a time, you should use the Package sequence parameter. This controls the order of execution of the maintenance packages, ensuring they are processed sequentially, one after the other.
Question 10
You want to set up a scenario for regular maintenance. The first event should take place after 1 year; after that, it is a regular cycle of 6 months. Which parameter do you have to use to map this in the system?
A. Maintenance package offset
B. Maintenance plan category
C. Shift factor
D. Scheduling indicator
Correct Answer: A
Explanation:
In SAP Plant Maintenance (PM), when setting up a maintenance plan that has a specific starting point for the first event and regular cycles afterward, the maintenance package offset is used to define the gap between the first event and subsequent maintenance events.
A. Maintenance package offset
This is correct. The maintenance package offset is used to define the time difference between the first maintenance event (which should happen after a set time, such as 1 year) and subsequent recurring maintenance events (which occur at regular intervals, such as every 6 months). The offset ensures that the first maintenance event is scheduled as a specific number of days (or months) from the start date, and after that, the system will schedule subsequent events at regular intervals based on the cycle defined.
B. Maintenance plan category
This is incorrect. The maintenance plan category defines the type of maintenance plan being used (such as time-based or performance-based), but it does not specify the interval or offset between maintenance events. While the plan category is important for defining the maintenance strategy, it does not directly control the scheduling of events with specific offsets or cycles.
C. Shift factor
This is incorrect. The shift factor is used to adjust the timing of maintenance activities when there are delays or when maintenance activities need to be moved forward or backward by a certain percentage. It is not used to define the regular cycle or the offset between the first and subsequent maintenance events.
D. Scheduling indicator
This is incorrect. The scheduling indicator in SAP PM is used to specify how the maintenance dates are calculated, such as whether they are based on a specific time, performance, or a counter. While the scheduling indicator can impact how maintenance events are calculated, it does not directly control the offset or specific cycle durations between events.
To set up a scenario where the first maintenance event occurs after 1 year and subsequent events happen every 6 months, you should use the maintenance package offset. This ensures the first event happens at the correct time and that subsequent events follow a regular cycle.
Top Training Courses
SPECIAL OFFER: GET 10% OFF
This is ONE TIME OFFER
A confirmation link will be sent to this email address to verify your login. *We value your privacy. We will not rent or sell your email address.
Download Free Demo of VCE Exam Simulator
Experience Avanset VCE Exam Simulator for yourself.
Simply submit your e-mail address below to get started with our interactive software demo of your free trial.