Use VCE Exam Simulator to open VCE files
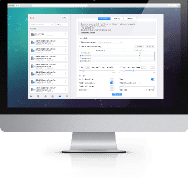
C_TS452_2022 SAP Practice Test Questions and Exam Dumps
What are the key benefits of using a stock transport order instead of a stock transfer posting between two plants? (Select three.)
A. You can record goods receipt in consignment stock.
B. You can plan the delivery costs in the system.
C. You can record goods receipt as consumption.
D. You can generate stock transport requisitions through material requirements planning (MRP).
E. You can issue goods from inspection stock.
Correct Answers:
B. You can plan the delivery costs in the system.
D. You can generate stock transport requisitions through material requirements planning (MRP).
E. You can issue goods from inspection stock.
Explanation:
A Stock Transport Order (STO) is an important tool in the procurement process within SAP. It is used to manage the movement of goods between two plants within the same company, and it provides several advantages over simpler stock transfer postings. Here’s why the correct answers are as follows:
B. Planning delivery costs – A Stock Transport Order allows you to plan and manage the costs related to the transportation of goods between plants. This is crucial for managing overall logistics and ensuring cost transparency, which is not easily done in a simple stock transfer posting.
D. Creating stock transport requisitions via MRP – With a Stock Transport Order, you can integrate it with Material Requirements Planning (MRP). This enables automatic generation of stock transport requisitions based on material needs, improving procurement efficiency and ensuring that stock levels are maintained across plants.
E. Issuing from inspection stock – A Stock Transport Order allows goods to be moved from inspection stock if they are being transferred from one plant to another, ensuring that quality checks are performed before goods are shipped.
Why the other options are incorrect:
A. Goods receipt in consignment – A Stock Transport Order doesn't directly relate to consignment stock, as consignment stock involves a different business process in which ownership is not transferred until goods are used.
C. Goods receipt to consumption – A goods receipt to consumption is typically used for items that are consumed directly and does not specifically relate to the Stock Transport Order process, which is more concerned with movement and storage of stock.
In summary, a Stock Transport Order helps streamline the transfer process, plan delivery costs, generate requisitions through MRP, and issue goods from inspection stock, providing more flexibility and visibility compared to a simple stock transfer posting.
Question 2
When entering a supplier invoice for a purchase order that has already been delivered, aside from the purchase order, which documents can be used as a reference? (Select two.)
A. Inbound delivery
B. Delivery note
C. Goods receipt
D. Bill of lading
Correct Answers:
A. Inbound delivery
C. Goods receipt
Explanation:
When processing a supplier invoice for a purchase order (PO) that has already been delivered, you can use various reference documents to ensure the accuracy of the transaction and verify that the goods were delivered as expected. Here’s why the correct answers are:
A. Inbound delivery – The inbound delivery is an important document that provides details of the goods that were delivered by the supplier to your organization. This document helps to ensure that the goods receipt matches the invoice and purchase order. It is used to track the physical delivery of goods and match them with the received quantities.
C. Goods receipt – The goods receipt (GR) document is created when goods are physically received in the system, and it is an essential reference for supplier invoice processing. The GR serves as confirmation that the goods have been delivered and provides details of quantities and conditions, which can be cross-checked with the supplier invoice.
Why the other options are incorrect:
B. Delivery note – While a delivery note is useful in the delivery process, it is not directly referenced when entering an invoice. It provides details of what the supplier intended to deliver but lacks the formal system integration and accounting features of the goods receipt or inbound delivery.
D. Bill of lading – A bill of lading is a legal document used in the transport of goods and is not commonly referenced when processing supplier invoices in an ERP system like SAP. It is useful for shipping and logistics purposes but not typically used as a reference for processing the invoice against the purchase order.
In summary, the inbound delivery and goods receipt are the primary references for processing supplier invoices in SAP. They ensure that the invoiced amount corresponds to the actual delivery and receipt of goods.
You have established a value contract with a supplier for packaging, but the exact materials and their respective prices will only be determined when the release orders are placed.
Which item category should you use when creating the contract?
A. W (Material group)
B. M (Material unknown)
C. B (Limit)
D. T (Text)
Correct Answer: C. B (Limit)
Explanation:
In the context of procurement contracts within SAP, the item category defines how the procurement process is managed for each item. When you are setting up a value contract where the exact materials and prices are not specified until later (at the time of creating release orders), the B (Limit) item category is the most appropriate choice. Here’s why:
C. B (Limit) – This item category is used when a value contract is created, and the contract specifies a total value (or limit) for the items. The exact details of the materials, quantities, and prices are only determined when the release orders are placed against the contract. In this case, the contract doesn’t specify materials or prices upfront, making B (Limit) the best match.
Why the other options are incorrect:
A. W (Material group) – This item category is used when a procurement contract is based on a material group, but in your case, the contract is for packaging, and the specific materials and their prices are determined later, so it is not suitable.
B. M (Material unknown) – This item category is used when the material is unknown and is typically used in cases like framework agreements where the material details are not known at the time of creating the contract. However, the B (Limit) category is more fitting for contracts where you’re working with a predefined total value, as in this case.
D. T (Text) – This item category is used when only text items are involved, such as services or informational notes. It is not suitable for contracts where goods or materials are involved.
In summary, for value contracts where specific materials and prices are not determined until later, the B (Limit) item category should be used to manage the overall value of the contract.
Which of the following are characteristics of the subcontracting procurement process? (Select three.)
A. You can post a non-valuated goods receipt for a subcontracting order item.
B. You can configure control parameters for the subcontracting item category.
C. You can generate subcontracting purchase requisitions through MRP.
D. You can assign a subcontracting order item to an account.
E. You can maintain the components to be provided in a bill of materials.
Correct Answers:
A. You can post a non-valuated goods receipt for a subcontracting order item.
B. You can configure control parameters for the subcontracting item category.
C. You can generate subcontracting purchase requisitions through MRP.
Explanation:
In the subcontracting procurement process, a company typically provides materials to a subcontractor, who then performs a manufacturing or assembly process on the materials and returns the finished goods. Subcontracting involves specific procedures within SAP to ensure that the process is managed efficiently. Here’s why the correct answers are:
A. You can post a non-valuated goods receipt for a subcontracting order item – In the subcontracting process, when goods are received from the subcontractor, it is possible to post a non-valuated goods receipt. This means that the value of the goods is not directly accounted for in the system at the time of receipt, as the value will only be recognized later when the final goods are received.
B. You can configure control parameters for the subcontracting item category – In SAP, the item category for subcontracting (often denoted as Subcontracting or L in SAP terms) has control parameters that can be customized. These parameters determine how procurement and inventory movements are handled, such as how materials are issued to the subcontractor, whether stock is transferred, etc.
C. You can generate subcontracting purchase requisitions through MRP – In the subcontracting process, Material Requirements Planning (MRP) can be used to automatically generate purchase requisitions for subcontracting. This helps ensure that the necessary materials are available and that the procurement process is aligned with the manufacturing needs of the subcontractor.
Why the other options are incorrect:
D. You can assign a subcontracting order item to an account – Typically, subcontracting order items are not assigned directly to a specific account. Instead, they are related to the materials and services being provided. This option doesn’t directly apply to the subcontracting process.
E. You can maintain the components to be provided in a bill of materials (BOM) – The components to be provided to the subcontractor are maintained as part of the subcontracting process, but this is usually done in the subcontracting order itself rather than through a Bill of Materials. The subcontracting order specifies the components and materials to be provided to the subcontractor.
In summary, the subcontracting procurement process is designed to allow companies to manage the receipt of goods from subcontractors, configure item category controls, and automatically generate purchase requisitions through MRP. These features help streamline the procurement and manufacturing processes.
How can you automatically update the conditions in an existing purchasing info record?
A. Check the Info Update indicator while maintaining a contract.
B. Check the Info Update indicator while creating a purchase order.
C. Check the Info Update indicator while maintaining a quotation.
D. Check the Info Update indicator while creating a contract release order.
Correct Answer: B. Check the Info Update indicator while creating a purchase order.
Explanation:
In the procurement process within SAP, the Purchasing Info Record (PIR) is a record that stores data about a supplier’s materials or services. When you want to automatically update the conditions in a purchasing info record, you can make use of the Info Update indicator. Here’s how this works:
B. Check the Info Update indicator while creating a purchase order – When you create a purchase order in SAP, and if the Info Update indicator is checked, the system will automatically update the corresponding purchasing info record with the latest conditions such as price, delivery times, and other terms from the purchase order. This helps maintain up-to-date records for future procurement transactions.
Why the other options are incorrect:
A. Check the Info Update indicator while maintaining a contract – While contracts are important for managing agreements with suppliers, they do not directly update the purchasing info record in the same manner as a purchase order would. The Info Update indicator is generally associated with purchase orders, not contracts.
C. Check the Info Update indicator while maintaining a quotation – A quotation is typically used to collect offers from suppliers, and while it may influence the final purchase order, the Info Update indicator is not associated with quotations for updating info records.
D. Check the Info Update indicator while creating a contract release order – Similar to a contract, a release order is typically linked to a contract but does not update the info record automatically. It's the purchase order itself that ensures updates to the purchasing info record.
In summary, checking the Info Update indicator during purchase order creation is the correct approach to ensure that the purchasing info record is automatically updated with the most current conditions. This helps to maintain accurate and up-to-date data for all procurement transactions.
You have entered into a cleaning contract with a supplier for your facility, where a fixed monthly amount has been agreed upon. You want to automatically generate a credit note every month. Which option should you use in this scenario?
A. Value contract
B. Invoicing plan
C. Scheduling agreement
D. Blanket purchase order
Correct Answer: B. Invoicing plan
Explanation:
In procurement, an invoicing plan is a tool used to automate the billing process based on predefined terms, such as the agreement for recurring payments. In this case, since you have agreed on a fixed monthly amount for cleaning services, an invoicing plan is the most appropriate tool to automatically generate the credit note every month.
Here’s why:
B. Invoicing plan – The invoicing plan allows you to set up regular, recurring payments, such as monthly charges for a service like cleaning. It provides the flexibility to automate invoicing (and credit note creation, if needed) based on the agreed terms in the contract. The invoicing plan can be configured to generate invoices or credit notes at regular intervals (e.g., monthly). This meets the requirement of automatically creating a credit note every month based on the contract terms.
Why the other options are incorrect:
A. Value contract – A value contract is an agreement where a total value is defined, but specific quantities and dates are not set. While a value contract is useful for certain types of procurement, it does not provide the automation needed for regular credit note generation. It’s more suitable for purchases based on a value threshold rather than periodic payments.
C. Scheduling agreement – A scheduling agreement defines delivery schedules and is used to procure materials or services over time, but it doesn’t focus on the automatic creation of invoices or credit notes. It’s better suited for materials procurement rather than service contracts.
D. Blanket purchase order – A blanket purchase order is used for a range of materials or services, often with a predefined quantity over a certain period. While it’s helpful for managing long-term purchases, it does not automate the invoicing process as efficiently as an invoicing plan for recurring services like cleaning.
In summary, for a contract that involves a fixed, recurring payment (such as cleaning services) and requires automatic credit note generation every month, an invoicing plan is the best tool to achieve this automation.
Which steps can be included in a subcontracting process? (Choose three.)
A. Invoice the subcontractor for the components consumed.
B. Purchase components for direct delivery to the subcontractor.
C. Create a sales order for components to be provided.
D. Create an outbound delivery for components to be provided.
E. Post subsequent adjustments for component consumption.
Correct Answer:
B. Purchase components for direct delivery to the subcontractor.
D. Create an outbound delivery for components to be provided.
E. Post subsequent adjustments for component consumption.
Explanation:
In the subcontracting process within procurement, the goal is to send materials to a third-party subcontractor who performs specific services or manufacturing processes. Here’s an explanation of each option:
B. Purchase components for direct delivery to the subcontractor – In a subcontracting process, you often purchase the required components (materials) and directly deliver them to the subcontractor for processing or assembly. This is an integral part of subcontracting as the supplier provides only the labor or additional processing needed for the goods.
D. Create an outbound delivery for components to be provided – Creating an outbound delivery is an essential part of the logistics process when the components are being delivered to the subcontractor. This step tracks the movement of goods from the company to the subcontractor, ensuring proper documentation and accounting of the items sent out.
E. Post subsequent adjustments for component consumption – After the subcontractor has used the components in their work, it is necessary to post any adjustments to reflect the actual consumption of components. This ensures accurate inventory and financial records.
Why the other options are incorrect:
A. Invoice the subcontractor for the components consumed – Typically, it is the company that is invoiced by the subcontractor for the services rendered, not the other way around. The subcontractor’s role is to process or assemble, not to charge for materials consumed.
C. Create a sales order for components to be provided – A sales order is typically used for customer transactions, not for managing subcontracting processes. In subcontracting, you deal with purchase orders and deliveries, not sales orders.
In summary, the steps that can be part of the subcontracting process include purchasing components for direct delivery, creating an outbound delivery for the materials, and posting subsequent adjustments for the components consumed.
What must you do when using supplier consignment? (Choose two.)
A. Create consignment storage locations.
B. Settle liabilities for consignment stock withdrawals.
C. Create consignment info records.
D. Settle liabilities for consignment stock receipts.
Correct Answer:
A. Create consignment storage locations.
B. Settle liabilities for consignment stock withdrawals.
Explanation:
Supplier consignment is a process where a supplier provides goods that are stored at the buyer’s location, but the buyer only pays for the goods as they are used. It allows the buyer to have immediate access to the materials without the full financial burden until they are consumed. Here’s what needs to be done in this process:
A. Create consignment storage locations – When using supplier consignment, you need to set up consignment storage locations in your inventory system to manage goods that are owned by the supplier but stored at your site. These locations track the consigned stock separately from your owned inventory.
B. Settle liabilities for consignment stock withdrawals – In consignment stock management, the buyer is only liable for the goods once they are withdrawn for use. Settling liabilities refers to recording and paying for the consigned items as they are used in the production or service process.
Why the other options are incorrect:
C. Create consignment info records – While consignment info records can be useful, they are not a mandatory step in the consignment process itself. These records contain information related to consignment stock, but the actual storage location and liability settlement are more critical to the process.
D. Settle liabilities for consignment stock receipts – Consignment stock receipts refer to goods being delivered by the supplier to your consignment storage location, and no liability is incurred at this stage. The payment liability is only triggered when you withdraw the stock for use, not when it is received.
In conclusion, when using consignment stock, it's essential to create consignment storage locations to manage the inventory and settle liabilities when you withdraw the stock for consumption or use.
You create a blanket purchase order for various minor repairs that might take place throughout the year. Which pieces of data must be entered when creating this order? (Choose two.)
A. Overall limit value
B. Invoicing plan type
C. Account assignment category
D. Net purchase order price
Correct Answer:
A. Overall limit value
C. Account assignment category
Explanation:
A blanket purchase order is typically used when a company expects to receive a series of deliveries or services over time but doesn't know the exact quantities or details upfront. It's often used for items like minor repairs, maintenance, or recurring services.
When creating a blanket purchase order, two important pieces of information must be specified:
A. Overall limit value – The overall limit value is the maximum amount of money the company is willing to spend over the course of the contract or order. This ensures that the costs are controlled, and any excess expenditure can be flagged. Since the exact amount of each repair is not known in advance, a limit is specified to manage spending.
C. Account assignment category – The account assignment category is used to specify how the purchase order is to be charged. This could involve specific cost centers, internal orders, or asset accounts that will bear the cost of the repairs, helping allocate the financial responsibility for the purchases.
Why the other options are incorrect:
B. Invoicing plan type – While invoicing plans are used in some purchase orders, they are not a mandatory requirement for blanket purchase orders. Invoicing plans typically apply to orders that have scheduled deliveries and payments, which is not always the case for blanket orders.
D. Net purchase order price – Since a blanket purchase order is used when the exact purchase price is not known upfront, entering a net purchase order price is generally not required. Instead, the total expenditure is capped by the overall limit value.
Which actions are possible when posting a goods receipt to stock referencing a purchase order? (Choose three.)
A. Record a goods receipt for part of the order quantity.
B. Record the received quantity into quality inspection stock.
C. Split the received quantity across multiple storage locations.
D. Adjust the purchase order quantity to match the received quantity.
E. Specify a value for the quantity received.
Correct Answer:
A. Record a goods receipt for part of the order quantity.
B. Record the received quantity into quality inspection stock.
C. Split the received quantity across multiple storage locations.
Explanation:
When posting a goods receipt (GR) to stock in reference to a purchase order (PO), it is essential to properly track and manage the receipt of goods. The GR process typically involves the physical receipt of goods and recording them in the system, matching them with the purchase order. Here are the possible actions:
A. Record a goods receipt for part of the order quantity – It's common to receive only part of an order at one time, especially in large or split deliveries. A goods receipt can be posted for partial quantities to reflect the delivery that has occurred. This ensures that the inventory is updated accurately, even if the entire order hasn't been fulfilled yet.
B. Record the received quantity into quality inspection stock – Upon receipt of goods, some items may require inspection before they can be used. These goods can be placed in a quality inspection stock to be checked for compliance or quality standards before being moved to the regular stock.
C. Split the received quantity across multiple storage locations – If your warehouse has multiple storage locations, the received goods can be split and stored in different areas. This is particularly useful for items that need to be stored according to type, size, or other logistical criteria.
Why the other options are incorrect:
D. Adjust the purchase order quantity to match the received quantity – The purchase order quantity should remain fixed once it’s created, regardless of the actual goods receipt. Adjustments to the PO quantity are typically handled by creating additional purchase orders or amendments, not through the goods receipt.
E. Specify a value for the quantity received – When posting a goods receipt, the quantity received is determined by the actual physical delivery, not by entering a specific value. The value is calculated based on the goods received and the agreed-upon price from the purchase order.
In summary, when handling a blanket purchase order, specifying the overall limit value and account assignment category is crucial for controlling spending and assigning the right cost responsibility. When posting a goods receipt, you can record partial receipts, place items in quality inspection stock, and split the quantity across multiple storage locations for better inventory management.
Top Training Courses
SPECIAL OFFER: GET 10% OFF
This is ONE TIME OFFER
A confirmation link will be sent to this email address to verify your login. *We value your privacy. We will not rent or sell your email address.
Download Free Demo of VCE Exam Simulator
Experience Avanset VCE Exam Simulator for yourself.
Simply submit your e-mail address below to get started with our interactive software demo of your free trial.