Use VCE Exam Simulator to open VCE files
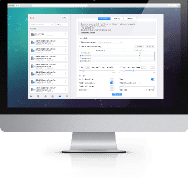
C1000-132 IBM Practice Test Questions and Exam Dumps
Question No 1:
What information can be updated in the Master PM application for an associated Preventive Maintenance record (PM)?
A. Work Order Status
B. PM Forecast
C. Generate Work Orders
D. PM Hierarchy
Answer: B
Explanation:
The Master PM (Preventive Maintenance) application is used for managing preventive maintenance tasks and records. In many asset management systems, the Master PM contains all the necessary details for scheduling and tracking preventive maintenance activities for equipment or assets. It also helps ensure that maintenance activities are performed regularly, reducing downtime and improving asset longevity.
Let’s break down each option:
A (Work Order Status): The Work Order Status typically refers to the state or progress of a work order related to a maintenance task (e.g., "In Progress," "Completed," "Closed"). While the Work Order Status is essential for tracking the progress of maintenance work, it is not typically something you would update directly within the Master PM application. Work orders are usually generated from the PM record, and the status of the work order is tracked separately.
B (PM Forecast): The PM Forecast can be updated in the Master PM application. The forecast provides a schedule for upcoming preventive maintenance tasks, often based on the time intervals defined for the maintenance activities (e.g., daily, weekly, monthly). The Master PM allows users to modify these forecasts based on changes to maintenance schedules, asset conditions, or other factors. This helps keep the maintenance plan up-to-date and ensures tasks are scheduled appropriately.
C (Generate Work Orders): The Master PM application typically has the functionality to automatically generate work orders based on the preventive maintenance schedule. However, this is a function that is triggered from the Master PM record, not something that you directly "update" in the Master PM itself. It's more of an action or process rather than a field or attribute to update.
D (PM Hierarchy): The PM Hierarchy often refers to the organizational structure or relationships of PM records, such as grouping preventive maintenance tasks for an entire asset, equipment, or location. While the hierarchy might be important for understanding how PM tasks are structured, it’s not something that is frequently updated in the Master PM record itself. It’s more of a structural reference.
Given the above explanations, the PM Forecast is the correct option as it directly relates to the scheduling and planning functions that can be modified within the Master PM application. Updating the PM forecast allows for better maintenance planning and resource allocation.
Question No 2:
When creating a new Inspection form, a client requires a Work Order to be created if certain responses are recorded. Which two actions are required for this to be achieved? (Choose two.)
A. Choose Work Order on question action.
B. Make the question response interactive.
C. In Form Settings add an Action Script.
D. In the Question Options, set the Require action flag.
E. Create an escalation on the QRESPONSE Object.
Correct Answers: A and C
Explanation:
When creating an inspection form where a work order needs to be created based on specific responses, certain steps need to be taken to trigger the creation of the work order. Let's analyze each option:
This is one of the required actions. When you define a question in the inspection form, the system needs to know that a specific action should be taken based on the response to that question. By choosing Work Order as the action for the question, you instruct the system that when certain conditions are met in the form (such as a particular answer), a work order should be automatically created. This is an essential configuration to trigger work order creation.
Making the question response interactive could be beneficial for enhancing user experience but does not directly relate to the creation of a work order based on responses. Making the question interactive might allow for more dynamic user input, but it is not necessary for triggering a work order creation. The system can still function without interactivity as long as the appropriate action is set (such as creating a work order).
An Action Script is essential to trigger more complex logic or behavior, such as creating a work order based on certain conditions in the form. By adding an Action Script to the form settings, you can specify detailed instructions and conditions under which the work order will be created. This script can define the conditions tied to responses, ensuring that a work order is created when those conditions are met. This is a necessary step to implement the required functionality.
Setting the Require action flag ensures that a specific action needs to be taken based on the answer provided. While it is useful for certain scenarios, it does not directly define what that action will be (such as creating a work order). The key to creating a work order lies in defining the specific action (like selecting Work Order for the question action) and using an Action Script to handle the logic behind that action.
Creating an escalation on the QRESPONSE Object is generally related to triggering alerts or escalating issues based on responses. While this can be useful for tracking or notifying about specific conditions in the responses, it is not directly related to creating a work order. Escalations would be used for alerting or notifying, not for automating the creation of a work order.
To achieve the client's requirement of creating a work order based on responses in the inspection form, the two necessary actions are A (choosing Work Order on the question action) and C (adding an Action Script in the form settings). These two steps ensure that the correct action is triggered and that the system is instructed to create a work order when specified conditions are met.
Question No 3:
In which three applications can Asset Depreciation be configured? (Choose three.)
A. Chart of Accounts
B. Tools
C. Asset Templates
D. Locations
E. Assets
F. Item Master
Correct answer: C, E, F
Explanation:
Asset depreciation is a critical aspect of asset management, and it can be configured in various parts of an enterprise resource planning (ERP) system. Let's look at the different applications listed and their relevance to configuring depreciation:
While the Chart of Accounts is important for financial accounting and helps categorize assets and liabilities, it is not typically where asset depreciation is configured. Depreciation settings are more specific to the asset management module and the asset itself, not the overall accounting structure. Thus, this is not a primary location for depreciation configuration.
The Tools application may contain utilities for performing general system maintenance or configurations, but it is not typically where asset depreciation settings are defined. Depreciation is usually set in asset-specific or asset-related applications, not in general tools.
This is one of the correct answers. Asset Templates define the characteristics of different asset types, including their depreciation methods. By configuring depreciation in asset templates, you can standardize depreciation settings across various assets that follow the same depreciation rules. This makes it easier to manage and track the depreciation process for different assets.
While Locations may be used to track where assets are physically located, they are not typically used to configure depreciation. Depreciation is related to the asset's accounting and management settings, not its physical location. Therefore, this is not a key area for configuring depreciation.
This is another correct answer. Depreciation is typically configured and applied directly to individual Assets within the asset management module. Each asset can have its own depreciation rules, such as the depreciation method (e.g., straight-line, declining balance), useful life, and salvage value. Therefore, depreciation is often configured at the asset level, allowing it to be tracked and calculated for each specific asset.
The Item Master is used to manage and track inventory items. While it is primarily concerned with product information, in certain systems, the Item Master can also be used to define attributes related to fixed assets, including depreciation settings. If an asset or item is considered part of the fixed asset inventory, depreciation settings may be configured here as well.
The correct answers are C (Asset Templates), E (Assets), and F (Item Master). These are the key applications where asset depreciation can be configured, allowing for effective management of asset-related financial calculations.
Question No 4:
How is the Lock Out / Tag Outs application structured?
A. Specify a Lock Out on an Asset with a Locking Device and define the Tag Out Operations.
B. Specify a Lock Out on the Location or Asset and define the Tag Out Operations.
C. Specify a Tag Out on the Location or Asset and define the Lock Out Operations.
D. Define the isolation procedures on a set of related assets and specify a sequence.
Correct Answer: B
Explanation:
The Lock Out / Tag Out (LOTO) process is a crucial safety procedure aimed at preventing accidental machine startups or the release of hazardous energy during maintenance and repair work. The process typically involves two components:
Lockout: The physical locking of a device (such as a switch or valve) to prevent equipment from being turned on or activated.
Tagout: The use of a physical tag to indicate that equipment should not be operated, even though the equipment may not be physically locked out.
Understanding the structure:
In a Lock Out / Tag Out application, there are two key components:
Lock Out: The isolation of the equipment or machinery, which usually involves placing a physical lock (such as a padlock) on a switch, valve, or other control device to ensure that the machinery cannot be turned on.
Tag Out: The practice of tagging the equipment with a warning sign or tag to indicate that the machinery should not be operated, even if the physical lock is not applied.
Now, let's review the options:
A. Specify a Lock Out on an Asset with a Locking Device and define the Tag Out Operations.
This option is incorrect because while it mentions specifying a lockout on an asset, it focuses only on a locking device and does not correctly emphasize that the lockout and tagout need to be defined in relation to the location or asset where the procedure is applied. Tagout operations need to be linked with the lockout process, but the structure should include both a lockout and a tagout on a location or asset.
B. Specify a Lock Out on the Location or Asset and define the Tag Out Operations.
This option is correct because it accurately reflects the structure of a Lock Out / Tag Out application. In most cases, a lockout is specified on a location or asset (i.e., the equipment or system that needs to be isolated), and the tagout operations are defined to indicate that the equipment should not be operated, even when locked out. This helps prevent accidental startup or release of hazardous energy.
C. Specify a Tag Out on the Location or Asset and define the Lock Out Operations.
This option is incorrect because it reverses the typical process. The lockout is usually performed before a tagout. While both lockout and tagout are related and used together, the lockout procedure should be defined before the tagout in the isolation process.
D. Define the isolation procedures on a set of related assets and specify a sequence.
This option is incorrect because it focuses too much on the isolation procedures for related assets and their sequence. While defining isolation procedures and their sequence is important, the core Lock Out / Tag Out structure involves defining the lockout and tagout on individual locations or assets, not necessarily on a set of related assets as a whole.
The correct structure involves specifying both the Lock Out and Tag Out procedures on a location or asset, which allows for clear identification of what equipment is isolated and ensures that it is not operated during maintenance. Therefore, Option B is the correct answer.
Question No 5:
When creating a labor record, what must be associated with it?
A. User Record
B. Person Record
C. Crew
D. Supervisor
Answer: B
Explanation:
In many systems, especially in workforce management, project management, or human resource management systems, a labor record is typically used to track the work done by an individual. To accurately capture and manage labor-related data, certain key associations need to be made when creating a labor record.
Here’s a breakdown of each option:
A. User Record:
While a user record may be involved in systems where user authentication and roles are important, it is not necessarily a required association when creating a labor record. The user record is more likely to be linked to system access, settings, and permissions rather than directly to the work done or labor recorded.
B. Person Record:
This is the correct answer. A person record is essential for linking a labor record to a specific individual. The person record typically contains personal details, such as the individual’s name, employee ID, role, and other relevant information. Associating a person record with a labor record ensures that the system knows exactly who performed the work and allows for accurate tracking, reporting, and management of labor activities.
C. Crew:
While crew might be associated with labor records in certain contexts (for example, if the work involves a group of people), the person record is the fundamental record that must be associated with a labor record. A crew is typically used when organizing work for multiple individuals, but it is not mandatory to link a crew when creating a labor record. A crew is a more specific association that may be useful in certain scenarios.
D. Supervisor:
A supervisor may be associated with labor records for oversight or approval purposes, but it is not necessarily required when initially creating a labor record. The supervisor’s role is generally to review or validate labor records, but the person record is the primary requirement for tracking the work of an individual.
In summary, the person record is the essential association when creating a labor record because it ensures that the labor performed is accurately attributed to a specific individual. This record includes the individual’s details and enables the system to properly track and manage their work. Therefore, B: Person Record is the correct answer.
Question No 6:
What are three available associations in the Hazards application? (Choose three.)
A. Lock Outs
B. Material Safety Data Sheets (MSDS)
C. Hazardous Materials
D. Tag Outs
E. Precautions
F. Safety Plans
Answer: B, C, F
Explanation:
In the context of the Hazards application, which is commonly used in industries that deal with safety management and risk assessment, there are several key associations that help manage and document the safety protocols related to various hazards. Let’s break down each option to see which three are commonly available associations in this kind of application.
A. Lock Outs
Lockouts are a safety procedure used to ensure that dangerous machines or equipment are properly shut off and cannot be started up again before maintenance or repair work is completed. While lockouts are important in managing hazards, they are usually considered a procedure or safety measure rather than a direct association in many hazard management applications. The emphasis here is more on hazard identification and management rather than specific safety measures like lockouts. Therefore, this is less likely to be considered one of the core associations in the Hazards application.
B. Material Safety Data Sheets (MSDS)
Material Safety Data Sheets (MSDS) provide detailed information about the properties, hazards, and safe handling of chemicals and materials. In the Hazards application, MSDS is a crucial association, as it helps users access and manage data regarding hazardous substances, ensuring safety protocols are followed. MSDS is typically available in many safety applications as a reference for handling materials safely, so this is definitely one of the available associations.
C. Hazardous Materials
Hazardous Materials are substances that pose a risk to health, safety, and the environment. These materials need to be managed carefully, and a Hazards application would typically have an association dedicated to tracking hazardous materials, their associated risks, and necessary safety measures. Therefore, hazardous materials would be one of the core associations in the application, allowing users to identify, document, and manage these materials in various processes.
D. Tag Outs
Similar to lockouts, tagouts are another procedure used to ensure that equipment is properly shut off and cannot be operated while it’s being serviced. While tagouts are important for hazard management, they are generally considered procedures rather than associations in hazard management applications. Thus, Tag Outs is less likely to be listed as an association in the application.
E. Precautions
Precautions are preventive actions or guidelines designed to avoid hazards or reduce their severity. While precautions are part of a safety plan, they may not typically be listed as a separate association in hazard management software. They might be included as part of safety measures within the application but aren't usually categorized as a standalone association in many hazard management applications.
F. Safety Plans
Safety Plans are documents that outline procedures and protocols to address various risks and hazards in a workplace or process. These plans often include steps to mitigate hazards, emergency response procedures, and other important safety measures. Since safety plans are integral to hazard management, they are commonly found as one of the core associations in hazard management applications. This allows users to refer to and follow detailed plans for managing identified risks and hazards.
In conclusion, the three most common available associations in the Hazards application would be Material Safety Data Sheets (MSDS), Hazardous Materials, and Safety Plans. These associations are essential for documenting, tracking, and managing various hazards and ensuring workplace safety. Therefore, the correct answers are B, C, and F.
Question No 7:
In the Assets application, a used engine needs to be replaced with a rebuilt engine. How might the rebuilt engine inherit the depreciation schedule from the used engine?
A. Use the action Exchange Depreciation Schedules.
B. Use the action Copy Depreciation Schedules.
C. Use the action Swap Depreciation Schedules.
D. Use the action Split Depreciation Schedules.
Answer: B
Explanation:
In asset management systems, such as the Assets application, depreciation schedules are crucial for tracking the value loss of assets over time. When an asset like an engine is replaced (for example, a used engine is replaced with a rebuilt engine), you may want the new asset to continue with the same depreciation schedule as the previous one to maintain consistency in accounting and reporting.
Now, let's look at the different options for inheriting the depreciation schedule from the used engine to the rebuilt engine:
A. Use the action Exchange Depreciation Schedules: This option is unlikely to be correct, as "exchange" suggests a swap or replacement of depreciation schedules between two different assets, which does not align with inheriting a schedule for the same asset type after a replacement.
B. Use the action Copy Depreciation Schedules: This is the most appropriate action. Copying depreciation schedules allows the rebuilt engine to inherit the same depreciation details, such as useful life, method, and any accumulated depreciation, from the used engine. This ensures consistency and minimizes manual adjustments to the depreciation schedule.
C. Use the action Swap Depreciation Schedules: Similar to option A, "swap" implies exchanging the depreciation schedules between two assets, which may not be appropriate in this case where you simply want the new asset (the rebuilt engine) to continue with the same depreciation schedule as the old one. This option would typically be used if two assets were being swapped with each other, not replaced.
D. Use the action Split Depreciation Schedules: "Splitting" depreciation schedules usually refers to dividing a single asset’s depreciation into separate components or time periods, which is not the goal here. The rebuilt engine needs to inherit the entire depreciation schedule of the used engine, not split it.
Therefore, the correct answer is B. Use the action Copy Depreciation Schedules, as this option allows the rebuilt engine to inherit the depreciation schedule from the used engine seamlessly, ensuring the continuity of depreciation tracking.
Question No 8:
The IoT Connector provides Maximo Manage, Maximo Health, and Maximo Predict the ability to connect to which two data sources? (Choose two.)
A. Maximo Spatial
B. Maximo Assist
C. IBM Watson IoT Platform
D. Maximo Safety
E. Maximo Monitor
Answer: C ,E
Explanation:
The IoT Connector in IBM Maximo enables the integration of various data sources with the Maximo suite of applications, such as Maximo Manage, Maximo Health, and Maximo Predict. This connector facilitates the connection to external systems and platforms that provide critical data, enabling real-time monitoring and predictive insights into asset health, performance, and usage.
Let's analyze the two correct answers:
IBM Watson IoT Platform (C): The IBM Watson IoT Platform is a powerful cloud-based service designed for integrating Internet of Things (IoT) devices, collecting data from them, and enabling advanced analytics. It provides a robust connection for IoT data to Maximo Manage, Maximo Health, and Maximo Predict. By integrating this platform, organizations can leverage the capabilities of IoT devices to monitor equipment, track performance, and predict failures. This connection is essential for predictive maintenance and real-time asset management.
Maximo Monitor (E): Maximo Monitor is an application in the Maximo suite designed to monitor the condition of assets and provide real-time feedback based on data collected from sensors and IoT devices. It can be used in conjunction with Maximo Health and Maximo Predict for continuous monitoring and analyzing asset data. By connecting Maximo Monitor to these applications, organizations can gain insights into asset health, enabling predictive maintenance and improving operational efficiency.
Now, for the incorrect options:
Maximo Spatial (A): Maximo Spatial is used for geospatial analysis, integrating GIS (Geographic Information System) data with Maximo. While it can provide valuable location-based insights, it is not primarily connected through the IoT Connector. Instead, it interacts with asset and work management functions in Maximo for tasks like asset location tracking and mapping.
Maximo Assist (B): Maximo Assist is an application that offers guidance for field workers by providing step-by-step instructions and operational data. It is not directly integrated through the IoT Connector. Instead, it typically uses Maximo Manage and other Maximo applications for work orders and asset management.
Maximo Safety (D): Maximo Safety is used to manage workplace safety, including incident management, safety audits, and compliance. It is not typically connected to the IoT Connector in the same way as IoT-specific platforms such as IBM Watson IoT Platform or Maximo Monitor.
In conclusion, the two data sources that the IoT Connector integrates with Maximo Manage, Maximo Health, and Maximo Predict are IBM Watson IoT Platform (C) and Maximo Monitor (E).
Question No 9:
What combination of information on a Work Order is used to create a histogram in the Graphical Scheduling application?
A. Craft/Skill Level Quantity and Hours
B. Labor and Crew Hours
C. Craft Quantity and Hours
D. Crew Work Group Quantity and Hours
Answer: D
Explanation:
The Graphical Scheduling application is designed to visualize and manage work schedules effectively by creating various types of charts, such as histograms, which are often used to display the allocation of resources, labor, or tasks over time. To generate a histogram that reflects resource utilization, it is essential to have specific information about the workforce, the quantity of labor, and the hours worked.
Let’s go through each option to understand the combination of data necessary to generate a histogram:
A. Craft/Skill Level Quantity and Hours – This option refers to information about the specific craft or skill level required for the work and the associated quantity of workers and hours. While this data is important for scheduling, it does not directly relate to generating a histogram that tracks the distribution of work over time. A histogram in Graphical Scheduling is more effective when focusing on specific work groups and their hours rather than just skill levels.
B. Labor and Crew Hours – This choice includes labor and crew hours, which are crucial for understanding the time spent by labor and crews on tasks. However, it doesn't specifically include information about the quantity of workers or work groups, which are necessary components for generating a histogram showing resource allocation over time. Labor and crew hours alone may be insufficient without the detailed breakdown by work group or crew type.
C. Craft Quantity and Hours – While this combination of craft and quantity with hours is useful for managing the specific types of work and hours allocated, it still lacks the work group or crew distinction. In practice, histograms in graphical scheduling typically require more detailed data related to work groups and teams, not just individual craft or skill types.
D. Crew Work Group Quantity and Hours – This is the correct combination for generating a histogram in the Graphical Scheduling application. Crew work groups are organized teams of workers that perform the tasks, and the quantity of workers in these groups combined with their hours provides a clear picture of resource utilization over time. This data helps to generate histograms that show the workload distribution among different work groups and the time periods during which they are active. The graphical representation will reflect the intensity and spread of labor across different work groups, making this combination the best choice for creating an accurate and informative histogram.
In conclusion, the correct combination for creating a histogram in the Graphical Scheduling application is D, as it includes the necessary data about crew work groups, quantity, and hours, which is essential for visualizing labor distribution and resource planning in a time-based graphical format.
Question No 10:
What is a core application in Maximo Manage?
A. Maintenance Version Control
B. Customer Billing
C. Permit to Work
D. Graphical Scheduling
Correct answer: C
Explanation:
Maximo Manage is a comprehensive enterprise asset management (EAM) solution by IBM that helps organizations manage and maintain their physical assets, such as machinery, equipment, and infrastructure. Among its many core applications, Permit to Work is an essential feature of the Maximo Manage suite. This application is designed to help organizations manage safety-critical operations and ensure compliance with industry standards for safe working conditions.
The Permit to Work application allows organizations to control and manage the processes related to issuing, tracking, and ensuring that workers follow safety protocols when performing tasks that could pose risks to health and safety. It ensures that workers have the necessary permits before they perform any work that may involve hazardous conditions, such as working in confined spaces, electrical work, or hot work (e.g., welding). This helps in maintaining safety standards and reducing risks.
Let's review why the other options are not core applications in Maximo Manage:
A. Maintenance Version Control: While version control for maintenance is an important aspect of asset management, it is not specifically a core application in Maximo Manage. Maximo does offer various tools for tracking and managing asset performance and maintenance, but version control is typically handled in a more granular manner through other configurations or integrations.
B. Customer Billing: Maximo Manage primarily focuses on asset and work management. Customer billing is not typically part of the core features of Maximo Manage, though it may be included as part of specific implementations or integrations with financial systems. This functionality is more commonly found in systems dedicated to customer relationship management (CRM) or enterprise resource planning (ERP).
D. Graphical Scheduling: While Maximo Manage does provide some scheduling capabilities, graphical scheduling is not specifically a core application. Maximo offers work order management, preventive maintenance scheduling, and asset tracking. However, graphical scheduling, which allows users to visualize and manage tasks in a Gantt chart or similar view, is typically an optional feature or module in Maximo, often integrated with the broader IBM Maximo Scheduler product.
In conclusion, Permit to Work is the core application in Maximo Manage, focusing on managing work safety and compliance, making it a critical function in ensuring operational safety and regulatory adherence in industries such as manufacturing, energy, and utilities.
Top Training Courses
SPECIAL OFFER: GET 10% OFF
This is ONE TIME OFFER
A confirmation link will be sent to this email address to verify your login. *We value your privacy. We will not rent or sell your email address.
Download Free Demo of VCE Exam Simulator
Experience Avanset VCE Exam Simulator for yourself.
Simply submit your e-mail address below to get started with our interactive software demo of your free trial.