Use VCE Exam Simulator to open VCE files
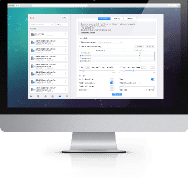
CLTD APICS Practice Test Questions and Exam Dumps
Question No 1:
Which of the following shipment modes is the most prone to packaging and product damage?
A Air
B Truck
C Water
D Rail
Correct Answer: C
Explanation:
Among the various modes of shipment—air, truck, water, and rail—water transport is the most prone to causing damage to packaging and products. This is due to several factors associated with the nature of shipping goods over large bodies of water.
Water transport involves moving goods across oceans or large seas, typically using cargo ships. These ships often face rough sea conditions, including heavy waves and unpredictable weather. The movement of the ships can lead to shifting of cargo, which increases the risk of damage to both packaging and products. Since goods are often stacked in containers, the force of the water and movement of the ship can cause pressure on items, leading to potential crushing or abrasion. Moreover, in some instances, if the cargo is not properly secured, items can shift inside the container, increasing the likelihood of damage.
While air transport is generally faster and more controlled, it often involves strict handling procedures that ensure the safety of goods. Items are typically handled by air cargo services with more care to prevent damage, and products are usually packed securely to withstand the limited turbulence and short shipping duration.
Truck transport and rail transport are less prone to damage compared to water transport. Trucks typically travel on paved roads and are easier to monitor and adjust for optimal load placement, which can reduce the risk of shifting during transit. Rail transport, while it might experience some jostling due to track conditions, is generally considered stable, and goods are typically well-secured.
However, water transport remains the most challenging due to its exposure to unpredictable external conditions, including ocean swells, storms, and the inherent movement of the vessels. Therefore, water transport carries the highest risk of packaging and product damage compared to other shipping methods.
Question No 2:
When importing goods such as fruit and produce into the United States (U.S.), which government agency is responsible for protecting agriculture from harmful pests and diseases?
A Food Safety and Inspection Service (FSIS)
B Food and Drug and Administration (FDA)
C U.S. Customs and Border Protection (CBP)
D Farm Service Agency (FSA)
Correct answer: C
Explanation:
The protection of agriculture from harmful pests and diseases is a critical responsibility to ensure the health and safety of the U.S. food supply and the environment. In the context of importing goods such as fruit and produce, the correct agency responsible for this task is U.S. Customs and Border Protection (CBP).
U.S. Customs and Border Protection (CBP) is tasked with preventing the introduction of harmful pests, diseases, and other threats through imported goods. CBP works closely with other agencies such as the Animal and Plant Health Inspection Service (APHIS), which is a division of the U.S. Department of Agriculture (USDA). APHIS specifically handles the inspection of agricultural products at U.S. borders, ensuring that produce, plants, and other agricultural goods do not bring in foreign pests or diseases. This is particularly important for fruits and produce, as they are susceptible to infestations that could threaten local crops and the environment.
Now, let's analyze the incorrect options:
A. Food Safety and Inspection Service (FSIS)
The Food Safety and Inspection Service (FSIS) is part of the USDA and is responsible for ensuring that meat, poultry, and processed egg products are safe, wholesome, and accurately labeled. While FSIS plays a crucial role in food safety, it is not responsible for preventing the introduction of pests and diseases through agricultural imports like fruits and produce.
B. Food and Drug Administration (FDA)
The Food and Drug Administration (FDA) regulates food safety, including certain aspects of produce, but its focus is more on ensuring that food is safe for consumption, particularly when it comes to processed foods and food additives. The FDA does not directly handle the inspection of agricultural products for pests and diseases, which is the focus of APHIS and CBP.
D. Farm Service Agency (FSA)
The Farm Service Agency (FSA) provides support to farmers and ranchers, including administering farm programs and providing financial assistance. The FSA does not handle the inspection of agricultural imports for pests or diseases. Its responsibilities are more focused on supporting U.S. farmers and agricultural communities.
In conclusion, U.S. Customs and Border Protection (CBP) is the agency responsible for protecting U.S. agriculture from harmful pests and diseases when goods like fruit and produce are imported into the country. CBP ensures that imported products meet safety and health standards, including preventing agricultural pests and diseases from entering the U.S.
Question No 3:
Under what circumstances should management generally consider utilizing qualitative forecasting techniques?
A When real-time data flow is available
B When historic data is both clear and relatively stable
C When developing strategic-level forecasts
D When demand is dependent on bill of material (BOM) calculations
Correct Answer: C
Explanation:
Qualitative forecasting techniques are often used when there is insufficient or unreliable historical data, or when the forecast involves strategic decision-making where expert judgment, intuition, or subjective assessments are more appropriate than purely data-driven methods. These techniques are typically used when there is a lack of quantitative data or when forecasting for long-term, uncertain, or new situations. Let's review the options to better understand why C is the correct answer:
A (When real-time data flow is available):
When real-time data flow is available, quantitative forecasting methods, such as time series analysis or statistical models, are typically more effective because they rely on actual data that can be tracked and analyzed in real-time. Qualitative forecasting is more commonly applied when the data is limited or non-existent, such as in scenarios involving new products or uncertain future conditions. Therefore, real-time data flow does not generally favor qualitative techniques, making this option less appropriate.
B (When historic data is both clear and relatively stable):
If historic data is both clear and stable, quantitative forecasting techniques are often preferred. Quantitative methods rely heavily on clear, stable, and historical data to identify patterns, trends, and relationships that can then be projected into the future. In such situations, quantitative models (e.g., moving averages, exponential smoothing) provide more precise and data-driven forecasts. Qualitative techniques are not typically necessary when there is stable and clear historical data available for analysis, so this option is not suitable.
C (When developing strategic-level forecasts):
Strategic-level forecasts typically look far into the future, where there may be a significant amount of uncertainty or lack of historical data. In these cases, qualitative forecasting techniques are often used. These techniques involve expert judgment, market research, surveys, focus groups, and other subjective inputs. The goal is to incorporate human insight and experience to predict long-term trends, opportunities, or challenges in situations where quantitative models may not be as effective or reliable. Therefore, qualitative methods are particularly appropriate in strategic forecasting, where future conditions are uncertain and difficult to model with historical data alone.
D (When demand is dependent on bill of material (BOM) calculations):
Bill of materials (BOM) calculations are more closely associated with quantitative forecasting techniques because BOM data involves detailed and specific calculations regarding the materials needed for production. This information is typically used in manufacturing environments to predict material needs based on historical consumption data, production schedules, and other measurable variables. Qualitative techniques are not typically used in this context, as the forecasting process relies heavily on quantitative data and calculations.
In conclusion, qualitative forecasting techniques are most useful when developing long-term, strategic-level forecasts where uncertainty and a lack of historical data make quantitative methods less effective. This makes C the correct answer.
Question No 4:
A carrier's costs are driven by equipment movement rather than shipment weight. Which of the following rates would be most appropriate for the carrier to utilize in charging its customers?
A Incentive rates
B Any-quantity rates
C Freight all kind (FAK) rates
D Per-car and per-truckload rates
Correct answer: D
Explanation:
When determining which rate structure is most suitable for a carrier, it’s important to consider the factors that drive the carrier’s costs. In this scenario, the carrier's costs are driven by equipment movement rather than the weight of the shipment. This suggests that the cost of transporting goods is more influenced by the movement and use of the transportation equipment (e.g., trucks, cars, containers) rather than the actual weight of the goods being shipped. Let's break down each option to determine the best fit:
Option A: Incentive rates
Incentive rates are typically designed to encourage certain behaviors or actions, such as volume shipping or early payment, rather than reflecting the carrier's cost structure. These rates are often used to reward customers for specific actions and don't necessarily align with the cost-driven approach focused on equipment movement. Therefore, incentive rates are not the best choice for a carrier whose costs are based on equipment use.
Option B: Any-quantity rates
Any-quantity rates are designed for shipments where the rate applies regardless of the size or weight of the shipment, as long as the shipment falls within certain guidelines. While this rate structure simplifies pricing for shipments, it does not specifically address a scenario where equipment movement is the primary cost driver. In cases where equipment use is a key factor, this type of rate may not adequately reflect the carrier's actual costs.
Option C: Freight all kind (FAK) rates
FAK rates are used to consolidate different types of freight under one general rate, regardless of the specific classification of goods. This type of rate is beneficial when there are various kinds of goods being shipped and the carrier wants to simplify pricing. However, like incentive and any-quantity rates, FAK rates are generally not tied directly to equipment movement. While they offer simplification, they do not target the issue of equipment usage being the primary cost driver.
Option D: Per-car and per-truckload rates
Per-car and per-truckload rates are the most appropriate for a carrier whose costs are driven by equipment movement. These rates charge based on the use of an entire car (for rail transport) or truck (for road transport) regardless of the weight of the shipment. Since the carrier's costs are primarily tied to the use of the transportation equipment (whether the truck is fully loaded or not), charging based on the equipment being used (per-car or per-truckload) aligns well with the carrier's cost structure. This rate system ensures that the carrier is compensated for the equipment use, not necessarily the weight of the cargo.
In conclusion, Option D: Per-car and per-truckload rates is the most appropriate rate structure because it directly aligns with the carrier's cost model, which is based on equipment movement rather than the shipment weight. This structure ensures that the carrier covers its costs for using the transportation equipment, which is the main driver of its expenses.
Question No 5:
A customer is looking to purchase a product from a company. Which of the following outputs of outbound order management would the customer consider primary?
A Order cycle time
B Logistics operations responsiveness
C Postsale logistics support
D Product availability
Correct answer: D
Explanation:
When a customer is considering purchasing a product from a company, product availability is typically the most critical factor in the decision-making process. This refers to whether the product the customer desires is in stock and can be delivered when requested.
Let's analyze each option to understand why D is the most relevant:
A – Order cycle time:
While order cycle time is an important metric for the company, it is not typically the primary concern for customers. Order cycle time refers to the time it takes from when an order is placed until it is fulfilled or shipped. Although customers may care about timely delivery, they are primarily focused on availability of the product they want to purchase rather than the specific speed of the order fulfillment process.
B – Logistics operations responsiveness:
Logistics operations responsiveness refers to how quickly and efficiently a company can handle logistics-related issues, such as responding to customer inquiries or managing inventory. While this is important for smooth operations, customers are less likely to focus on this directly when making a purchase decision. They care more about whether the product is available and when they can expect it, rather than the internal logistics responsiveness.
C – Postsale logistics support:
Postsale logistics support, which involves support after a purchase (such as handling returns, exchanges, or customer support), is certainly important for customer satisfaction. However, customers consider this factor only after the purchase is made. The primary concern before making a purchase is whether the product is available for purchase and can be delivered.
D – Product availability:
This is the most critical output from outbound order management that customers care about when deciding whether to purchase. If the product is not available, the customer cannot proceed with the purchase. The ability of the company to ensure that the desired product is in stock and ready for delivery is the primary concern for the customer. Without availability, the customer cannot complete the transaction, regardless of how fast the company can process the order or provide post-sale support.
In conclusion, product availability directly impacts the customer's ability to make a purchase, making D the correct answer.
Question No 6:
From a health and safety perspective, which of the following sets of parameters must be taken into account when considering manual material handling?
A Task, working environment, equipment, and individual capacity
B Task, load, layout, and equipment
C Layout, load, working environment, and individual capacity
D Task, load, working environment, and individual capacity
Correct Answer: D
Explanation:
When considering manual material handling (MMH), several key factors must be taken into account to minimize the risk of injury and ensure safety. The correct set of parameters is Task, load, working environment, and individual capacity. Let’s break down why these four factors are critical:
Task: The type of task being performed (e.g., lifting, carrying, pushing, or pulling) significantly impacts the level of risk. Certain tasks may require more strenuous physical effort or may involve awkward postures, both of which can contribute to strain or injury. The nature of the task itself must be carefully analyzed to ensure that it is suitable for the individuals involved.
Load: The characteristics of the load—such as its weight, size, shape, and stability—are crucial considerations. A heavy, bulky, or unstable load can increase the risk of injury, especially if the material handling task requires awkward body positioning or high physical exertion.
Working environment: The physical conditions in which the task is carried out, including factors such as lighting, temperature, floor surface, space, and noise, are also critical. A cluttered or slippery environment, for instance, can increase the likelihood of accidents. Proper working conditions can help reduce unnecessary strain or risk during material handling.
Individual capacity: The physical capabilities of the worker must also be considered. This includes factors such as strength, fitness, and experience. Each individual may have different levels of physical capacity to handle loads safely, and tasks should be matched to their ability to prevent injury.
The other options are less comprehensive because they omit one or more of these critical factors:
A: While this option includes important parameters like task, working environment, and individual capacity, it lacks a focus on the load, which is fundamental to assessing manual material handling risk.
B: This option includes task, load, and layout, but it does not consider the working environment or individual capacity, both of which are key factors in ensuring safety and preventing injuries.
C: Although it includes layout, load, and working environment, it omits the task and individual capacity, which are both essential for understanding the risks associated with manual handling.
In summary, D is the most comprehensive and correct answer because it includes all four critical elements: task, load, working environment, and individual capacity, each of which plays a vital role in assessing and mitigating health and safety risks related to manual material handling.
Question No 7:
Which of the following categories is a weakness of the rail systems?
A. Safety records
B. Inflexible infrastructures
C. Effects of the weather
D. Routes from city centers
Correct answer: B
Explanation:
Rail systems, while offering efficient and reliable transportation, often suffer from several weaknesses that can affect their performance and flexibility. Among the options, inflexible infrastructures is the most significant weakness.
Inflexible infrastructures (option B) refers to the rigid nature of rail systems. Unlike other forms of transportation, such as buses or cars, rail systems are constrained by fixed tracks that cannot easily be rerouted or adjusted. This limitation makes it difficult to quickly adapt to changes in demand, shift services, or respond to unforeseen events. If there is a need to reroute a service or add a new connection, it requires significant time and resources to modify the infrastructure, making rail systems less adaptable to changing conditions.
Let’s consider the other options:
Safety records (option A) may sometimes be a concern, but generally, rail systems are known for having strong safety protocols. While accidents do happen, the safety record of railways tends to be better than other forms of transportation, particularly road vehicles. This makes safety records less of a weakness compared to other factors.
Effects of the weather (option C) are a concern for rail systems, as weather conditions such as snow, ice, and extreme temperatures can impact train schedules and infrastructure. However, rail systems have advanced technology and maintenance practices to mitigate weather-related disruptions, making it less of a pervasive weakness.
Routes from city centers (option D) can sometimes be an issue, particularly in cities with outdated or limited rail networks. However, many modern rail systems are designed to efficiently connect city centers with suburban or rural areas, so this isn't always a significant weakness.
Thus, the primary weakness highlighted here is B, as the inflexible nature of rail infrastructure can limit the system’s adaptability and responsiveness to changing needs or circumstances.
Question No 8:
Which of the following statements represents the primary function of inventory?
A. Make products available while minimizing total carrying cost
B. Realize economies of scale while minimizing total carrying cost
C. Reduce ordering cost while minimizing total carrying cost
D. Buffer against delivery time while minimizing total carrying cost
Correct Answer: A
Explanation:
The primary function of inventory is to ensure that products are available for customers when they need them, while minimizing the costs associated with holding that inventory. Let's break down the options to understand why A is the best answer:
A. Make products available while minimizing total carrying cost
This option correctly highlights the primary role of inventory. Inventory exists to meet demand and make products available for sale at the right time. At the same time, it’s crucial to manage the costs of holding inventory, known as carrying costs, which include storage, insurance, and depreciation. The goal is to strike a balance between having enough inventory to fulfill customer needs and not overstocking to the point where the carrying costs become too high. Thus, making products available while managing the associated costs is the key function of inventory.
B. Realize economies of scale while minimizing total carrying cost
This option is partially true in some cases but does not fully represent the primary function of inventory. Economies of scale refer to the cost advantages that a business can achieve by increasing production and lowering costs per unit. While this is a benefit of inventory management, it’s not the primary function. The primary purpose is to ensure availability of products and minimize costs, not necessarily to achieve economies of scale.
C. Reduce ordering cost while minimizing total carrying cost
This option focuses on ordering costs, which refer to the costs associated with placing and receiving orders. While it’s important to manage ordering costs in inventory management, the primary function is about making products available to meet demand. Reducing ordering costs is part of the broader strategy but not the main function of inventory.
D. Buffer against delivery time while minimizing total carrying cost
This option refers to inventory’s role as a buffer against fluctuations in delivery times or lead times. While inventory can serve as a buffer to prevent stockouts due to delays in supply, this is just one aspect of inventory management. The main focus is ensuring product availability and managing the overall costs associated with inventory, not just acting as a buffer for delivery time.
In conclusion, A is the best choice because it accurately captures the balance that inventory management aims to achieve: making products available when needed while keeping carrying costs low. This is the primary function of inventory in most business operations.
Question No 9:
Which of the following factors would be considered of strategic importance to a firm's logistics function?
A. A firm operates in a competitive oligopoly
B. Total cost of production
C. Production lead time
D. Order cycle time
Correct Answer: D
Explanation:
In logistics, strategic importance refers to factors that directly affect the efficiency, competitiveness, and overall performance of a firm in its supply chain. Among the options, order cycle time is the most critical factor in the logistics function. The order cycle time represents the total time from when a customer places an order to when the order is delivered. It directly influences customer satisfaction and can be a key differentiator in competitive markets.
Reducing the order cycle time helps improve the responsiveness of a firm to customer demand, which is crucial for maintaining customer loyalty, enhancing service levels, and gaining a competitive edge. Faster order cycle times can also lead to better inventory management, lower holding costs, and more efficient operations, making it a strategic concern for logistics functions.
Now, let’s look at the other options:
A. A firm operates in a competitive oligopoly: While the competitive environment in which a firm operates (such as an oligopoly) can influence logistics decisions, this factor alone is not directly related to the logistics function itself. The competitive structure might shape broader strategic decisions, but logistics is more focused on operational efficiency, customer service, and cost management.
B. Total cost of production: Although production costs are important, they fall more under the realm of manufacturing and overall operational costs rather than logistics specifically. Logistics focuses more on the distribution, transportation, and timely delivery of goods. The total cost of production is relevant but not as strategically important for logistics as factors like order cycle time or transportation efficiency.
C. Production lead time: Production lead time refers to the time taken to produce goods after an order is placed, which is a critical factor for manufacturers. However, it is not primarily a logistics function, though it does influence logistics decisions like inventory management and distribution planning. Logistics focuses more on delivery timelines, order fulfillment, and transportation rather than the production phase itself.
In conclusion, order cycle time directly impacts logistics operations and customer service, making it a strategically important factor in the logistics function. It is crucial for firms aiming to improve responsiveness and operational efficiency, thereby giving them a competitive advantage. Therefore, D is the correct answer.
Question No 10:
Which of the following lean tools would a warehouse team use to document, analyze, and improve the flow of information and materials to customers?
A. Lean six sigma
B. Kaizen
C. Value stream mapping
D. Five S methodology
Correct Answer: C
Explanation:
In the context of lean methodology, the primary focus is on improving efficiency by reducing waste and optimizing processes. Different lean tools and techniques can be used to address specific aspects of a process or workflow. When it comes to documenting, analyzing, and improving the flow of information and materials, one specific lean tool stands out for its ability to provide a visual map of the entire process from start to finish, which is value stream mapping.
Let’s break down each option to see why C is the best answer:
A. Lean six sigma: Lean Six Sigma is a methodology that combines the principles of lean (which focuses on eliminating waste and improving process efficiency) with Six Sigma (which focuses on reducing variability and defects). While it is an effective method for improving quality and processes, Lean Six Sigma is not a specific tool. It is more of an overarching methodology that uses a variety of tools, including value stream mapping, to identify areas for improvement. It is not the specific tool for documenting and analyzing flow in this scenario.
B. Kaizen: Kaizen refers to continuous improvement and involves small, incremental changes made over time. It is a philosophy and mindset rather than a tool. While Kaizen promotes ongoing improvements in various processes, including the flow of materials and information, it does not provide a direct method for documenting and analyzing the flow. Instead, it’s used to foster a culture of improvement and can complement other tools, like value stream mapping, to help identify areas that need change.
C. Value stream mapping: This is the correct answer. Value stream mapping (VSM) is a lean tool specifically designed to document, analyze, and improve the flow of materials and information in a process. It provides a visual representation of the entire process from the initial stages to delivery to the customer, identifying both value-adding and non-value-adding activities. By using VSM, a warehouse team can spot bottlenecks, inefficiencies, and areas where waste occurs, allowing them to make targeted improvements to streamline operations and improve flow.
D. Five S methodology: The Five S methodology focuses on organizing the workplace to improve efficiency and safety through the five steps: Sort, Set in order, Shine, Standardize, and Sustain. While it is an important lean tool for creating an organized and efficient work environment, it is more focused on physical organization rather than documenting or analyzing the flow of materials and information. It’s a complementary tool but does not directly address flow analysis.
In conclusion, value stream mapping is the most appropriate tool for documenting, analyzing, and improving the flow of information and materials in a warehouse setting. By using this tool, a warehouse team can gain a comprehensive understanding of their processes and identify key areas where improvements are needed to enhance efficiency and customer satisfaction.
Top Training Courses
SPECIAL OFFER: GET 10% OFF
This is ONE TIME OFFER
A confirmation link will be sent to this email address to verify your login. *We value your privacy. We will not rent or sell your email address.
Download Free Demo of VCE Exam Simulator
Experience Avanset VCE Exam Simulator for yourself.
Simply submit your e-mail address below to get started with our interactive software demo of your free trial.