Use VCE Exam Simulator to open VCE files
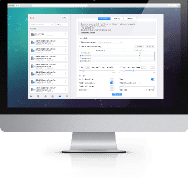
CPIM-BSP APICS Practice Test Questions and Exam Dumps
Question 1
In an income statement, to which category is the cost of goods sold most directly connected?
A. sales dollars
B. total inventory dollars
C. marketing expenses
D. manufacturing expenses
Correct answer: D
Explanation:
The cost of goods sold (COGS) is a key component of the income statement, and it represents the direct costs attributable to the production of the goods that a company sells. These costs typically include raw materials, direct labor, and manufacturing overhead — essentially, all expenses that are directly tied to the production of the goods themselves.
COGS is fundamentally related to manufacturing expenses because it includes the costs incurred in making a product ready for sale. For example, if a company manufactures furniture, the cost of the wood, the wages paid to workers who assemble the furniture, and the depreciation of equipment used in production would all be part of COGS. Therefore, option D is correct because it reflects the direct connection between the production process and the costs that are reported as COGS on the income statement.
Option A, sales dollars, is not a correct match for COGS, though sales revenue and COGS are both essential elements of the income statement. The difference between sales and COGS gives the gross profit, but they are not causally related. Sales figures indicate revenue generated, while COGS pertains to the expenses involved in producing what was sold. So although sales and COGS appear together in the income statement, they represent different aspects of business operations.
Option B, total inventory dollars, refers to the value of inventory on hand at a given time. While inventory data is used in the calculation of COGS (through the formula beginning inventory + purchases – ending inventory = COGS), inventory itself is not what COGS is directly related to. Rather, COGS reflects the portion of inventory that has been used or sold during the period.
Option C, marketing expenses, are part of the operating expenses, which are listed separately on the income statement under selling, general, and administrative expenses (SG&A). Marketing and promotional costs are not included in COGS, as they do not pertain directly to the production of goods but rather to efforts to sell those goods.
In summary, cost of goods sold is most closely aligned with manufacturing expenses because it includes all direct costs associated with producing products. These production-related expenses form the foundation of the COGS figure reported on the income statement. This makes manufacturing expenses the correct and most specific classification.
Question 2
Which of the following techniques is specifically used to identify the underlying cause of a problem rather than just its symptoms?
A. Statistical process control
B. Five whys
C. Scatter diagram
D. Pareto chart
Correct answer: B
Explanation:
The technique known as the "Five Whys" is a well-established method used in root cause analysis to identify the fundamental origin of a problem. It works by repeatedly asking the question "Why?"—typically five times—until the most basic cause of an issue is identified. This method is commonly used in quality improvement, manufacturing, healthcare, and other industries that require detailed problem-solving and continuous improvement.
The purpose of the Five Whys is not to treat surface-level symptoms but to dig deep into the process or system to discover what truly led to the undesirable outcome. For example, if a machine stopped working, asking "Why?" might lead to discovering that a part wore out. Asking "Why?" again could reveal that regular maintenance was missed, and so on. Each successive "Why?" reveals a deeper level of insight until the root cause is found, such as a failure in scheduling preventive maintenance.
Option A, Statistical Process Control (SPC), is a method that uses statistical tools to monitor and control a process. It helps detect process variation and maintain process stability, but it does not specifically aim to identify the root cause of a problem. Instead, it signals that something may be wrong, prompting further investigation.
Option C, Scatter diagram, is a visual tool that plots two variables on a graph to determine whether a relationship exists between them. While useful in identifying correlations or patterns, it does not provide a mechanism to drill down into the root cause of an issue.
Option D, Pareto chart, is another quality improvement tool that helps prioritize problems based on their frequency or impact. The chart is based on the Pareto principle (80/20 rule), which suggests that a small number of causes are often responsible for a large portion of the problem. While a Pareto chart can help identify which problems to address first, it does not delve into the root causes themselves—it identifies which issues are most frequent or impactful.
In contrast, the Five Whys is specifically designed for root cause analysis and helps practitioners avoid stopping at the first or most obvious answer. It encourages deeper thinking and a structured approach to discovering systemic weaknesses or breakdowns.
Therefore, the best answer to the question about which technique focuses on root cause analysis is the Five Whys.
Question 3
Which type of plant structure involves a single product being transformed into multiple different products at the following stage, indicating a divergent flow in the production process?
A. A-Plant
B. I-Plant
C. T-Plant
D. V-Plant
Correct answer: D
Explanation:
The correct plant type that matches the description of a production system where one product at an early stage diverges into multiple distinct end products at later stages is the V-Plant. This type of production structure is named for the visual shape of the letter “V,” representing how the flow starts from a single point and branches outward into several different pathways.
In a V-Plant, the production process begins with a common input or a generic product. As production progresses, this common input is split or customized into a variety of final products. This means that a single product or material is used to manufacture different items depending on subsequent processing steps. This model is common in industries where base materials or intermediate products are processed into specialized goods. For instance, in the food industry, a basic dairy product like milk may be used to produce cheese, yogurt, cream, or butter. In metallurgy, raw metal ingots may be shaped into various metal components such as rods, sheets, or wires.
Option A, the A-Plant, represents a convergent flow structure. This means multiple inputs are required to produce a single final product. It is the opposite of the V-Plant and is typically found in assembly operations, such as automobile manufacturing, where various parts and components come together to make one final item.
Option B, the I-Plant, describes a linear production flow with a one-to-one relationship between stages. Each stage processes the product sequentially without divergence or convergence. This type is typical for continuous manufacturing processes like oil refining or paper production.
Option C, the T-Plant, incorporates characteristics of both divergence and convergence. It begins with a base product or input and adds specialized components at later stages. This plant type supports both commonality at the start and differentiation as the product moves through stages, as in the case of computers that start with standard circuit boards and later have different modules or features added.
In contrast, the V-Plant is specifically about taking one generic product and splitting it into several different specialized outputs. It emphasizes variety emerging from a single point, which makes it distinct from the other types listed.
Thus, the best match for a production system involving a product that transforms into multiple distinct products at the next stage (divergent points) is the V-Plant.
Question 4
Which manufacturing process is best described as having a limited variety of standard products, minimal direct labor costs, and strong technical support during production?
A. Jobbing
B. Intermittent
C. Flow
D. Project
Correct answer: C
Explanation:
The flow manufacturing process, also known as continuous or mass production, is most accurately described by the characteristics mentioned in the question. Flow manufacturing is designed for the efficient, high-volume production of a narrow range of standardized products. The system is highly automated and organized in a way that materials and components move through a predetermined sequence of operations with minimal human intervention.
One of the defining features of flow manufacturing is its reliance on automation and machinery, which greatly reduces the need for direct labor. Instead of requiring skilled workers to complete complex, varied tasks, flow production uses machines and conveyor systems to perform repetitive operations. As a result, the cost of direct labor per unit is significantly lower compared to other manufacturing processes.
In addition, flow manufacturing requires a high level of technical support. Since the system depends heavily on precise machinery and coordinated production lines, technical specialists are needed to ensure that everything functions correctly, maintenance is performed regularly, and any mechanical issues are quickly resolved to prevent disruptions in the continuous flow.
Option A, jobbing, involves producing small batches of custom products, often requiring skilled labor and higher direct labor costs. Each job is different, so it does not benefit from standardization or economies of scale.
Option B, intermittent manufacturing, includes processes such as batch production. This system handles a moderate variety of products and tends to switch between product types, which means more setup time and less technical automation compared to flow manufacturing. Labor costs are usually higher, and technical support is important but not as central as in flow systems.
Option D, project manufacturing, applies to unique, large-scale, and complex tasks—like constructing a ship or building an aircraft. These are not repetitive or standardized products, and they typically involve high direct labor and significant customization. Technical support is crucial, but the nature of production is vastly different from what is described in the question.
In contrast, flow manufacturing focuses on producing a narrow set of standard items with speed, consistency, and low per-unit cost. The emphasis is on process efficiency and automation, supported by technical experts who maintain the systems rather than workers who craft products manually.
Thus, the manufacturing process that aligns with low direct labor costs, a narrow range of standardized products, and high technical support is flow manufacturing.
Question 5
Which production environment strategy involves products that require unique designs or significant levels of customization?
A. Make-to-order
B. Assemble-to-order
C. Make-to-stock
D. Engineer-to-order
Correct answer: D
Explanation:
The production strategy that involves products requiring a completely unique design or extensive customization is known as Engineer-to-Order (ETO). This strategy is specifically intended for cases where the product is not designed until after the order is received. In this model, every customer order triggers a new design, engineering, and manufacturing process tailored to that specific order. This is common in industries such as shipbuilding, aerospace, and large-scale industrial equipment where each item must meet detailed, customer-specific requirements.
In an Engineer-to-Order environment, the process typically begins with engineering activities. These may include concept design, CAD modeling, detailed specifications, and sometimes even prototyping. After the design is completed and approved by the customer, the actual manufacturing process starts. Because of the high degree of uniqueness and complexity involved, lead times tend to be longer, and the cost per unit is typically higher than in more standardized production environments. The value offered to the customer lies in the ability to fulfill very specific, often one-of-a-kind requirements that cannot be met with off-the-shelf or semi-customized products.
Option A, Make-to-Order (MTO), does involve customization but not at the level of ETO. In MTO, the product design is already established, and production begins after receiving the customer order. While products may be tailored to customer preferences (such as color, size, or optional features), the core product remains the same. MTO is often used in industries such as furniture or high-end consumer electronics, where configuration options exist but the engineering does not change for each order.
Option B, Assemble-to-Order (ATO), refers to a strategy where products are assembled from pre-manufactured components after the customer places an order. This allows some degree of customization but relies on existing modules or parts. For example, a computer company may offer customers the ability to choose different processors, memory sizes, and storage options, all of which are assembled into the final product after the order is received. ATO enables faster response times while still offering flexibility, but it does not involve any unique engineering or design.
Option C, Make-to-Stock (MTS), is the least customized environment. Products are manufactured based on demand forecasts and kept in inventory until customer demand arises. These products are standardized and mass-produced, such as bottled drinks, canned goods, or ready-made clothing. This strategy prioritizes speed and efficiency rather than customization.
In summary, among all the listed options, Engineer-to-Order is the only strategy that centers on unique design and significant customization, making it the correct answer. It is specifically tailored for projects that cannot begin until all specifications are defined and approved, making it ideal for highly specialized, one-off products.
Question 6
In the context of lean production, which type of layout is generally the most efficient for minimizing waste and maximizing flow?
A. Islands
B. Connected islands
C. Functional layout
D. Cells
Correct answer: D
Explanation:
In a lean production environment, the primary goal is to eliminate waste and enhance value by streamlining processes and improving the flow of materials and information. Among the various layout types used in manufacturing, the cellular layout—commonly referred to simply as "cells"—is widely regarded as the most efficient for achieving lean objectives.
A cellular layout groups together all the machines, tools, and workstations needed to manufacture a particular product or product family. These cells are designed to facilitate one-piece flow or small-batch production, meaning materials move through the process with minimal delay, inventory buildup, or transportation waste. This layout minimizes unnecessary motion and waiting time, both of which are major forms of waste according to lean principles.
One of the key advantages of cells is that they are typically arranged in a U-shape or another compact configuration that allows workers to easily monitor multiple machines or processes with minimal walking or material handling. This setup supports better communication, faster identification of problems, and quicker response to quality issues or process disruptions. It also enables cross-training of workers and more flexible staffing.
Option A, islands, refers to separate and isolated workstations or departments. This layout is generally inefficient for lean production because it creates silos, requires more material handling, and leads to longer lead times and higher inventory levels.
Option B, connected islands, is a slight improvement over isolated islands because there is some attempt to link workstations, often through manual transport or conveyors. However, it still lacks the integration and efficiency that a well-designed cellular layout provides.
Option C, functional layout, is organized based on the type of equipment or process (e.g., all drilling machines in one area, all milling machines in another). While this is useful for traditional manufacturing with varied and complex jobs, it is inefficient for lean production because it leads to long travel distances, increased work-in-process inventory, and poor flow.
By contrast, cells support the lean goal of continuous flow and make it easier to implement just-in-time production, reduce setup times, and improve overall responsiveness to demand. They also facilitate visual management and standardized work practices, which are foundational to lean operations.
Therefore, when striving for lean efficiency, the cellular layout stands out as the most effective and aligned with lean manufacturing principles.
Question 7
What is the meaning of the Japanese word "Gemba" in the context of production and operations?
A. shop floor
B. shop order
C. shop packet
D. shop traveler
Correct answer: A
Explanation:
The Japanese word Gemba (also spelled Genba) literally means "the real place" or "the actual place." In the context of manufacturing, business operations, and continuous improvement practices like Lean or Six Sigma, Gemba refers to the shop floor, or the place where the actual work is performed. This is where value is created — whether it be through assembling products, serving customers, or processing data.
In Lean management, the concept of Gemba is central to understanding how operations function in real time. Managers, supervisors, and improvement teams are encouraged to "go to the Gemba" — meaning they should visit the shop floor regularly to observe, engage with workers, identify inefficiencies, and discover opportunities for improvement. This practice is often referred to as the Gemba Walk. During a Gemba Walk, the focus is on observing processes firsthand rather than relying solely on reports or data summaries.
This principle is grounded in the idea that the most accurate understanding of problems and opportunities comes from direct observation. Problems are rarely fully understood from behind a desk. For instance, a production bottleneck might be better understood by seeing how a particular machine is functioning or how operators interact with it. In the same way, quality issues might be better analyzed by watching the inspection process and identifying where deviations occur.
Option A, shop floor, correctly reflects this concept. It refers to the physical location where production or service delivery occurs — where machines operate, workers assemble parts, and products take form. This is the Gemba, the “real place” of value creation.
Option B, shop order, refers to a document that authorizes work to be done — essentially a production order or job ticket. While it's related to manufacturing, it is not the actual place of work, and therefore not synonymous with Gemba.
Option C, shop packet, typically refers to a group of documents that travel with a job or order through the production process. It might include routing sheets, instructions, material lists, or inspection requirements. Again, this is documentation, not a physical place.
Option D, shop traveler, is similar to a shop packet in that it represents paperwork that follows a work order through the manufacturing steps. It provides traceability and instructions, but it is not a location and thus not equivalent to Gemba.
In summary, Gemba is a foundational term in Lean thinking and Japanese business philosophy. It emphasizes direct observation and engagement with real-world processes, making shop floor the accurate and contextually appropriate translation.
Question 8
In an assemble-to-order (ATO) manufacturing strategy, what type of items are typically included in the master production schedule (MPS)?
A. standard items
B. finished items
C. raw materials
D. subassemblies
Correct answer: D
Explanation:
In an assemble-to-order (ATO) production environment, the company waits to receive a customer's order before assembling the final product, but many of the components and parts used to build that product are pre-manufactured and stocked in advance. This approach offers a balance between customization and efficiency, allowing manufacturers to meet customer-specific requirements without the long lead times associated with make-to-order systems.
The master production schedule (MPS) plays a crucial role in managing this process. In an ATO system, the MPS does not typically include finished goods, because the final assembly happens only after an order is received. Instead, the MPS focuses on planning the production and inventory levels of subassemblies—the semi-finished components that are later combined to make the final customized product.
Subassemblies are standard parts that can be used in various product configurations. By scheduling and producing these subassemblies in advance, companies can respond quickly to customer orders without building up large inventories of finished goods. This leads to better responsiveness, reduced waste, and improved customer satisfaction.
Now let's examine why the other options are incorrect in this context:
Option A, standard items, is too vague and does not directly address the level of detail found in an MPS for an ATO environment. While subassemblies could be considered standard items, the term lacks the specificity needed to be the best answer.
Option B, finished items, would be appropriate in a make-to-stock (MTS) system where final products are produced based on forecasted demand and stocked in inventory. However, in an ATO environment, finished goods are not produced until an actual order is received, so they are not the focus of the MPS.
Option C, raw materials, are the basic inputs used in production. These are usually managed through material requirements planning (MRP), not directly in the master production schedule. The MPS focuses on higher-level items that are closer to the final product in the production hierarchy.
By contrast, option D, subassemblies, accurately reflects what is scheduled in the MPS under an assemble-to-order strategy. These components are ready to be quickly assembled into a finished product once a customer order is placed, making them the ideal level of planning in this type of environment.
Therefore, in an ATO system, the MPS must ensure the availability of subassemblies so that customer orders can be fulfilled efficiently and accurately. This makes subassemblies the correct and most logical focus of the master production schedule.
Question 9
Which of the following best describes a key feature of an intermittent manufacturing environment?
A. Work center load is predictable
B. Routings for all products are the same
C. Work centers are organized by function
D. Kanban is the most appropriate scheduling method
Correct answer: C
Explanation:
An intermittent manufacturing environment is one where production is carried out in small batches or lots rather than in a continuous flow. This type of system is commonly used when there is a high variety of products being produced in relatively low volumes. One of the fundamental characteristics of intermittent manufacturing is that the work centers are organized by function rather than by product line. This setup is also known as a process layout or functional layout.
Option C accurately reflects this structure. In a functionally organized layout, similar machines or operations are grouped together. For example, all drilling machines may be located in one area, all painting operations in another, and all welding stations in yet another. Products move between these functional areas based on their specific routing requirements. Because products often require different processes and sequences, the paths they take through the facility may vary significantly.
This arrangement provides flexibility and is ideal for customized or made-to-order products. However, it also makes scheduling more complex due to variable processing times and routing paths.
Option A, which states that work center load is predictable, is generally not true for intermittent manufacturing environments. Because of the wide range of products and varying routing requirements, workloads at each work center can fluctuate significantly. This unpredictability requires more active scheduling and workload balancing to avoid bottlenecks or idle time.
Option B, which claims that routings for all products are the same, is incorrect. In an intermittent environment, one of the defining features is that different products often have different routing paths through the factory. Unlike a flow line setup where all products follow the same sequence of steps, intermittent systems support routing flexibility to handle product variation.
Option D, which suggests that Kanban is the most appropriate scheduling method, is also not suitable in this context. Kanban is a pull-based scheduling system most commonly used in repetitive or continuous manufacturing environments such as Just-in-Time (JIT) systems. It relies on stable, predictable demand and consistent workflows, which do not align with the high variability and customization found in intermittent production.
In conclusion, the correct answer is that work centers in an intermittent manufacturing environment are organized by function. This allows for the flexibility needed to handle diverse products and varying production requirements. While this setup supports customization, it also introduces challenges related to scheduling, material handling, and work-in-process management.
Question 10
Which of the following practices would be most effective for a company aiming to reduce product defects during manufacturing?
A. Hansei
B. Jidoka
C. Muri
D. Heijunka
Correct answer: B
Explanation:
Among the choices listed, Jidoka is the concept most directly aimed at reducing defects in a manufacturing environment. Jidoka is a foundational principle of the Toyota Production System (TPS) and lean manufacturing, often translated as "automation with a human touch." It refers to the ability of machines and operators to detect problems immediately and stop production to prevent the defect from continuing down the line.
Jidoka involves two major elements:
The capability to automatically detect abnormalities or defects.
The empowerment of workers or machines to stop the process when a defect is found.
This concept ensures that quality is built into the process. When a problem is detected—such as a defect in a part, a missing component, or a process deviation—the system stops immediately. This prevents the defect from propagating through the rest of the production process, saving time, cost, and effort later on. It also allows teams to investigate the root cause and make corrections before resuming work, leading to long-term quality improvements.
Option A, Hansei, means "reflection" and is used to analyze mistakes or problems after they occur. While it's a valuable tool for continuous improvement, it is more reactive in nature rather than proactive. Hansei helps understand what went wrong and how to prevent it in the future, but it doesn’t directly stop defects from occurring in real-time.
Option C, Muri, refers to overburdening people or equipment. It's one of the three forms of waste (along with Muda and Mura) in lean systems. Reducing Muri can indirectly reduce defects caused by stress or overuse of machines, but it is not a specific method for identifying and eliminating defects.
Option D, Heijunka, refers to production leveling or smoothing. It is a method for reducing uneven workloads and improving flow. While Heijunka improves efficiency and consistency, it doesn’t specifically target the identification or prevention of defects.
Jidoka stands out because it directly embeds quality control into the production process. When combined with other lean practices such as standardized work, visual management, and continuous improvement (Kaizen), Jidoka forms a powerful defense against defective products reaching customers.
Therefore, for a firm focused on proactively identifying and eliminating defects during production, Jidoka is the most effective and appropriate concept.
Top Training Courses
SPECIAL OFFER: GET 10% OFF
This is ONE TIME OFFER
A confirmation link will be sent to this email address to verify your login. *We value your privacy. We will not rent or sell your email address.
Download Free Demo of VCE Exam Simulator
Experience Avanset VCE Exam Simulator for yourself.
Simply submit your e-mail address below to get started with our interactive software demo of your free trial.