Use VCE Exam Simulator to open VCE files
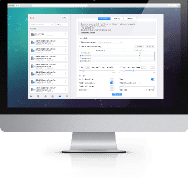
LSSBB Six Sigma Practice Test Questions and Exam Dumps
Question 1
A ___________ is used primarily to track the stability of the average value of a metric of interest.
A. NP Chart
B. Xbar-R Chart
C. I-MR Chart
D. C Chart
Answer: B
Explanation:
In Statistical Process Control (SPC), control charts are essential tools used to monitor and track the behavior of a specific process over time. Each chart type serves a different purpose depending on the type of data being measured and the specific aspect of the process being tracked.
The question focuses on tracking the stability of the average value of a metric, which directly points to a type of control chart that specifically monitors averages.
A. NP Chart:
The NP chart (Number of Defects chart) is used for attribute data where the number of defective items is tracked within a sample. It helps track the proportion of defective items, but it does not focus on monitoring the average value of a metric.
B. Xbar-R Chart:
The X-bar-R chart is specifically designed to monitor the average (X-bar) and the range (R) of a set of data points. It is particularly used when the process involves variable data (such as measurements) and tracks the stability of the average of the data. The X-bar chart monitors the central tendency of a process, ensuring that the process remains stable around the target mean value. This makes it the correct choice for tracking the average value of a metric.
C. I-MR Chart:
The I-MR chart (Individuals and Moving Range chart) is used to monitor individual measurements over time and their moving ranges. This chart is typically used when data is collected one point at a time (i.e., when sample sizes are 1). While it tracks individual values, it is not designed to specifically track the average of a metric but rather the individual measurements and their variability.
D. C Chart:
The C chart is used to track the count of defects or non-conformities in a fixed sample size. It is typically applied to attribute data when counting the number of defects, but it does not focus on the average value of a metric, making it irrelevant for this question.
The Xbar-R Chart is designed to monitor the average value of a metric and the variation around it, which is why it is the correct choice for tracking the stability of the average value of a process. Therefore, the correct answer is B.
Question 2
For her injection molding project a Belt needed to track the percentage of defectives of a particular sample set so she used a ___________ to display the data?
A. Individual Chart
B. C Chart
C. Xbar Chart
D. P Chart
Answer: D
Explanation:
In Statistical Process Control (SPC), the correct type of control chart depends on the type of data being collected. In this scenario, the Belt is interested in tracking the percentage of defectives in a sample set. Since this involves tracking the proportion of defective items in a given sample, the most appropriate chart to use is a P Chart.
Let’s examine each option:
A. Individual Chart:
The Individual Chart (often referred to as the I Chart) is used for tracking individual measurements. It is particularly useful when only one observation per sample is taken (i.e., sample size = 1). It is not suitable for tracking proportions of defectives, as it focuses on individual data points rather than the proportion of defective items within a sample.
B. C Chart:
The C Chart is used to track the count of defects in a fixed sample size, but it does not track proportions. It is designed for situations where the number of defects per unit is being counted, not the proportion of defectives. This makes it unsuitable for tracking percentages of defectives in sample sets.
C. Xbar Chart:
The Xbar Chart is used to monitor the average of a set of measurements. It is typically used with continuous data (variable data) where multiple measurements are taken at each sampling point. Since the question is about tracking the percentage of defectives, which is attribute data (counting the number of defective items), an Xbar Chart is not the correct choice.
D. P Chart:
The P Chart is designed specifically to track proportions or percentages of defectives in a sample. This type of chart is used for attribute data where the number of defectives (or non-conformities) is counted in each sample and the proportion of defective items is plotted. The P Chart is ideal for the scenario described, where the Belt needs to track the percentage of defectives in a sample set.
Since the task is to track the percentage of defectives in a sample set, the appropriate chart to use is the P Chart. Therefore, the correct answer is D.
Question 3
Which of these graphs demonstrates conditions which would be sufficient to enable OCAP for the process?
A. Xbar Chart
B. Time Series Chart
C. Neither
D. Both
Answer: A
Explanation:
OCAP (Operator Control and Adjustment Process) is a method used in process control that enables operators to intervene in a process to adjust and correct it, ensuring that it stays within acceptable limits. For OCAP to be effective, the graph or chart used should demonstrate a process that can be monitored for variability and trends so that operators can take corrective actions as needed.
Let’s evaluate each option:
A. Xbar Chart:
The Xbar Chart is part of Statistical Process Control (SPC) and is used to monitor the average value of a process over time. It is an essential tool in process monitoring because it helps track whether the process is staying within the specified control limits or if corrective actions are necessary. If the Xbar Chart shows a stable process (no significant variation outside control limits), it is a good indicator that OCAP can be applied. The chart enables operators to monitor trends and take necessary adjustments, making it a sufficient tool for enabling OCAP.
B. Time Series Chart:
A Time Series Chart simply tracks the changes of a process over time. While it does show trends, it is not specifically used for monitoring processes in the context of control limits. A time series chart typically shows raw data trends without the specific focus on control limits, so it is not typically used as a primary tool for enabling OCAP. For OCAP, the focus needs to be on understanding whether the process is in control and when intervention is necessary, which is more clearly indicated by control charts like the Xbar Chart.
C. Neither:
This option is incorrect because the Xbar Chart is indeed a suitable graph for enabling OCAP, making "neither" an invalid answer.
D. Both:
While a Time Series Chart can show trends, it does not inherently provide the necessary control limits or allow for effective process control adjustment in the same way the Xbar Chart does. Therefore, both is not the correct answer since the Time Series Chart does not demonstrate conditions sufficient for OCAP on its own.
The Xbar Chart is the appropriate tool for enabling OCAP because it allows operators to track the process's average and intervene when the process deviates beyond control limits. The Time Series Chart lacks the necessary control limits and is less effective for process control in this context. Therefore, the correct answer is A.
Question 4
Control Charts were developed by Dr. Shewhart to track data over time. To detect Special Cause variation the Control Charts use which of these?
A. Data shift analysis
B. Outlier analysis methods
C. Center Line and Control Limits
D. None of the above
Answer: C
Explanation:
Control Charts are a foundational tool in Statistical Process Control (SPC), developed by Dr. Walter A. Shewhart, to monitor and control processes over time. These charts are used to detect variations in a process, distinguishing between Common Cause (inherent, normal variation) and Special Cause (unexpected or irregular variation) factors.
The key to detecting Special Cause variation lies in how the data is plotted on the control chart and how the process is monitored. Control charts help identify when a process deviates significantly from its normal behavior, signaling that some external factor (a special cause) may be affecting the process. Let's analyze each option:
A. Data shift analysis:
While data shift analysis could be helpful in certain statistical analyses, it is not a primary method used in control charts to detect Special Cause variation. Control charts focus on detecting shifts in the process via control limits, not by manually analyzing shifts in data. Therefore, this is not the correct answer.
B. Outlier analysis methods:
Outlier analysis involves identifying data points that fall far outside the typical range of values. While outlier analysis can be useful in some statistical contexts, control charts are designed to detect Special Cause variation by monitoring the behavior of the process over time using control limits, not by simply identifying individual outliers. Outliers may indicate a potential special cause, but the primary method for detecting variation in control charts is the Center Line and Control Limits. Hence, this is not the best choice.
C. Center Line and Control Limits:
This is the correct method. Control charts feature a Center Line (typically the process average or target) and Control Limits (upper and lower bounds that represent the expected range of normal variation for the process). When data points fall outside of the control limits or show unusual patterns, it indicates the presence of Special Cause variation. This is the primary way control charts detect changes in the process that require investigation or corrective action. Therefore, this is the correct answer.
D. None of the above:
This option is incorrect because Center Line and Control Limits are the primary method for detecting Special Cause variation in control charts.
Control charts use the Center Line and Control Limits to track process behavior over time and detect Special Cause variation. When data points fall outside of the control limits or exhibit unusual patterns, it indicates that something external to the usual process might be affecting the process, and corrective action may be needed. Therefore, the correct answer is C.
Question 5
Common and ______________ Cause Variation are the focus of Statistical Process Control.
A. Uncommon
B. Ordinary
C. Special
D. Selective
Answer: C
Explanation:
Statistical Process Control (SPC) is a method used to monitor and control a process by tracking and analyzing variation in the process over time. The primary goal of SPC is to ensure that the process operates at its highest efficiency and produces consistent results. To achieve this, SPC distinguishes between two types of variation:
Common Cause Variation:
This is the inherent variation in a process that is stable and predictable. It is the natural, everyday variation that occurs in a system or process and is generally expected. Common cause variation reflects the usual operation of the process, and it is not typically something that can be fixed immediately. It is often considered "background noise" in the process and cannot be removed easily unless the system itself is redesigned.
Special Cause Variation:
This type of variation is caused by external factors or irregular events that disrupt the normal functioning of a process. Special causes are unexpected, and their presence signals that something out of the ordinary has occurred, requiring attention. These causes might include equipment failure, operator errors, or environmental changes. Special cause variation is not inherent to the process and should be addressed to restore normal functioning.
SPC focuses on identifying and analyzing both Common Cause and Special Cause variation to ensure that the process remains stable and predictable. When Special Cause variation is detected, it can be investigated and removed, while Common Cause variation is often something that needs to be managed, rather than eliminated.
Now, let's review the options:
A. Uncommon:
"Uncommon" is not a term used in SPC to describe variation. SPC focuses on distinguishing between Common and Special Cause variations, so this option is incorrect.
B. Ordinary:
While ordinary could describe something that is regular or typical, it is not the term used in SPC. SPC specifically addresses Common Cause and Special Cause variations, making "ordinary" not an appropriate term here.
C. Special:
This is the correct term. In SPC, the two types of variation that are the focus are Common Cause and Special Cause. Special Cause variation refers to variations that are due to external or abnormal factors that disrupt the process, and these need to be addressed for the process to return to stability.
D. Selective:
"Selective" does not refer to a type of variation in SPC. The correct terminology is Special Cause, so this option is incorrect.
In Statistical Process Control, the two main types of variation that are the focus are Common Cause variation and Special Cause variation. The correct term to complete the sentence is Special. Therefore, the correct answer is C.
Question 6
Special Cause Variation falls into which two categories?
A. Natural & Unnatural
B. Short Term & Long Term
C. Assignable & Pattern
D. Attribute & Discreet
Answer: C
Explanation:
In Statistical Process Control (SPC), special cause variation refers to the type of variation that is caused by external, unusual, or irregular factors that disrupt the normal functioning of a process. These causes are not inherent to the process and typically indicate that something abnormal or unexpected has occurred, requiring investigation and action.
Special cause variation can generally be categorized into two main types:
Assignable Cause Variation:
This is variation that can be traced to a specific, identifiable cause. Assignable causes are unusual or exceptional factors that are not part of the normal operation of the process. They are typically the result of factors like equipment malfunction, human error, changes in materials, or environmental influences. Once identified, these causes can often be corrected to bring the process back to normal. Assignable causes are also referred to as specific causes.
Pattern Cause Variation:
This refers to a pattern or trend in the data that indicates a special cause. For instance, repeated failures at certain times of day, or consistent errors with a particular batch of material, can indicate a pattern of special cause variation. It may not always be immediately obvious what the specific cause is, but the data shows a recognizable trend or pattern that suggests something unusual is affecting the process. This is often linked to cyclical or recurrent patterns that point to external disturbances.
Now, let's review the options:
A. Natural & Unnatural:
While the terms "natural" and "unnatural" might seem to describe types of causes, they are not typically used in the context of SPC to describe special cause variation. The appropriate terms are Assignable and Pattern. Therefore, this option is incorrect.
B. Short Term & Long Term:
These terms relate to time horizons rather than specific types of variation. While it's possible to consider the duration of variation, SPC focuses on the nature of the cause, which is why Assignable and Pattern are the more accurate terms for categorizing special cause variation.
C. Assignable & Pattern:
This is the correct answer. Assignable and Pattern are the two main categories used to describe Special Cause variation in SPC. Assignable causes are identifiable and can be corrected, while pattern causes refer to recurring trends or patterns that suggest abnormal influences affecting the process.
D. Attribute & Discreet:
These terms are related to data types and measurement scales (qualitative vs. quantitative), but they do not pertain to the categorization of special cause variation. Assignable and Pattern are the appropriate categories.
Special cause variation in SPC is most effectively categorized into Assignable and Pattern causes. Therefore, the correct answer is C.
Question 7
Range Charts are the technique used to determine if Special Causes are occurring within the subgroups of the ______________.
A. Histograms
B. SPC Charts
C. NP Charts
D. Pareto Charts
Answer: B
Explanation:
In Statistical Process Control (SPC), range charts (also known as R charts) are used to monitor the variation within the subgroups of a process over time. These charts help identify whether there are any special cause variations present that are affecting the process.
The purpose of an R chart is to track the range (the difference between the highest and lowest values) of data within each subgroup and to see if this variation is consistent or if there are any unusual shifts or patterns that would suggest an external or special cause impacting the process. If the range exceeds established control limits, it may indicate that something outside of normal process variation is affecting the output.
Let's break down the options:
A. Histograms:
Histograms are graphical representations of data distribution. They show the frequency of data within various ranges or bins but are not used specifically to track special causes within subgroups. Therefore, histograms are not the correct tool for identifying special causes within subgroups.
B. SPC Charts:
This is the correct answer. SPC Charts (Statistical Process Control Charts) are a family of charts used to monitor various aspects of a process, such as control charts, X-bar charts, and R charts. The Range Chart (R chart) specifically helps detect if special causes of variation are present within the subgroups of data.
C. NP Charts:
NP Charts (Number of Defects Chart) are used to track the number of defectives in a sample when the sample size is fixed. While NP charts are part of SPC, they are not used to track the range within subgroups. Therefore, NP charts are not the correct technique for detecting special causes within subgroups' variation.
D. Pareto Charts:
Pareto Charts are used to identify the most significant factors in a process based on the Pareto Principle (80/20 rule), which asserts that most problems are caused by a small number of factors. While Pareto charts are helpful in prioritizing issues, they are not used to track variation within subgroups or to detect special causes of variation. Therefore, Pareto charts are not applicable here.
Range charts (R charts) are specifically used within SPC charts to track variation and identify if special causes are occurring within the subgroups of a process. Therefore, the correct answer is B.
Question 8
If the production is for higher volume and monitoring and the Mean and variability is to be monitored for four machines producing product and the characteristic to be monitored is Variable Data, which SPC Chart is best to be selected?
A. Xbar-R Chart
B. Individual-MR Chart
C. NP Chart
D. CUSUM Chart
Answer: A
Explanation:
When monitoring a process where both the mean and variability need to be tracked, and when the data is variable (i.e., the data is continuous and measurable, like measurements of weight, length, temperature, etc.), the X-bar and R chart (often written as Xbar-R Chart) is the most appropriate choice.
Here's why:
X-bar and R Chart (Xbar-R):
This chart is specifically used when you are monitoring both the average (mean) and the range (variability) within a process, especially when the data is continuous (variable). The X-bar chart monitors the average of each subgroup, while the R chart monitors the variation (range) within those subgroups. This combination allows you to track both central tendency and dispersion of the data. It's ideal for situations where the production is in higher volume and multiple machines are being monitored. The Xbar-R Chart is widely used when you have subgroups of measurements, such as readings from four machines in your case, and need to assess the consistency and quality of the process.
Now let's consider the other options:
B. Individual-MR Chart (I-MR):
The Individual-Moving Range (I-MR) chart is used when the process data consists of individual measurements rather than subgroups. It's appropriate when you have a smaller sample size and need to monitor individual data points over time. Since you're dealing with four machines producing products (which suggests you have subgroups), the I-MR chart wouldn't be the best fit for this scenario.
C. NP Chart:
An NP chart is used to monitor the number of defective items in a sample when you have a fixed sample size. Since the data you are monitoring is variable and continuous (not count data), the NP chart would not be suitable for tracking the mean and variability of your measurements.
D. CUSUM Chart:
The Cumulative Sum (CUSUM) chart is used to detect small shifts in the process mean over time. It's sensitive to small changes, but it's generally used for processes that require quick detection of shifts. It's more complex and typically used for processes where detecting even a small change is crucial. However, for a higher-volume production process where both mean and variability are being monitored, the X-bar and R chart is still a more straightforward and common choice.
For monitoring both the mean and variability of a higher volume production process with four machines and variable data, the best SPC chart to use is the Xbar-R Chart (A).
Question 9
When a Belt Poka-Yoke's a defect out of the process entirely then she should track the activity with a robust SPC system on the characteristic of interest in the defect as an early warning system.
A. True
B. False
Answer: A
Explanation:
When a Belt applies Poka-Yoke (a mistake-proofing technique) to eliminate defects from a process entirely, it is important to continue monitoring the system with an SPC (Statistical Process Control) system. This is because even though the goal of Poka-Yoke is to prevent defects, tracking the characteristics of interest in the process remains critical for ensuring that the mistake-proofing solution is functioning properly and that the process remains stable over time.
Let's break this down further:
Poka-Yoke (Mistake-Proofing):
Poka-Yoke is a concept from Lean manufacturing designed to prevent errors before they happen. The primary goal is to design processes in such a way that it becomes impossible for defects to occur. For example, using physical safeguards, alarms, or automatic feedback mechanisms to prevent incorrect actions or inputs. When a defect is eliminated from the process entirely through Poka-Yoke, it's typically due to a change in the design or operational procedure.
SPC as an Early Warning System:
After implementing a Poka-Yoke, it is still crucial to monitor the process. This is because, even with mistake-proofing mechanisms in place, there could still be variations in the process that could lead to issues in the future. Statistical Process Control (SPC) is a powerful tool for continuously monitoring the process and providing early warnings if the process deviates from its desired state. By tracking key characteristics of interest (like measurements or performance indicators) in the SPC system, you can spot special causes of variation that could indicate an issue before it becomes a significant defect.
Importance of Tracking Post-Poka-Yoke:
Even though Poka-Yoke effectively prevents defects, maintaining an SPC system ensures that the process stays on track and that any subtle, unforeseen issues are detected early. This proactive approach ensures the longevity and sustainability of the improvements made. It also helps in detecting drift or shifts in process performance that could lead to new types of defects or quality issues, even after the defect has been initially eliminated.
In summary, while Poka-Yoke removes defects from the process, it is still necessary to monitor the process with a robust SPC system to track key characteristics and act as an early warning system for any potential future issues.
The correct answer is A, because tracking the activity with a robust SPC system is a proactive approach to ensuring that the process remains stable and continues to meet quality standards even after Poka-Yoke has been applied to eliminate defects.
Question 10
Following the completion of a LSS project the Belt not only creates a Control Plan he also develops a _____________ so those involved in the process know what to do when the critical metrics move out of spec.
A. Response Plan
B. Call List
C. Chain-of-Command
D. Defect Analysis Plan
Answer: A
Explanation:
In a Lean Six Sigma (LSS) project, the goal is not just to improve a process, but to sustain that improvement. After completing the project, it's important to not only create a Control Plan to monitor the ongoing performance of the process but also to develop a Response Plan for when critical metrics move out of spec.
Here's why:
Control Plan:
A Control Plan is a document that outlines how the process should be monitored to ensure it stays within the desired specifications. It includes details such as the key process parameters, the measurement methods, acceptable ranges, and who is responsible for tracking the metrics. The Control Plan ensures that the process remains stable after improvements are made.
Response Plan:
A Response Plan is a proactive plan that is developed alongside the Control Plan. It outlines the steps that should be taken when the process deviates from its desired state or when critical metrics move outside of specification (i.e., when the process goes out of control). This ensures that there is a clear course of action to address any issues before they become significant problems. It includes actions like identifying the root cause, containment strategies, corrective actions, and a plan to bring the process back in control.
The Response Plan helps to ensure that the team knows exactly what to do in case of an issue, which minimizes downtime and ensures quick resolution of any deviations. It is part of ensuring that the process remains stable and sustainable in the long term.
Call List:
A Call List is typically used for emergency situations or for contacting individuals when issues arise, but it does not provide a structured plan for addressing process deviations. While important for communication, it lacks the actionable detail that a Response Plan provides.
Chain-of-Command:
The Chain-of-Command defines the hierarchical structure of authority within an organization. While it’s important for overall organizational structure, it doesn't directly address what actions need to be taken when the process goes out of spec. A chain-of-command focuses more on decision-making and escalation rather than specific corrective actions.
Defect Analysis Plan:
A Defect Analysis Plan could be used to investigate the causes of defects but doesn't serve the same purpose as a Response Plan. It’s more focused on understanding the root causes of problems once defects have occurred, while the Response Plan is about managing immediate action when metrics go out of spec.
The correct answer is A, because the Response Plan ensures that there is a clear, actionable set of steps to follow when critical metrics go out of specification. It works in tandem with the Control Plan to keep the process stable and prevent the recurrence of issues.
Top Training Courses
SPECIAL OFFER: GET 10% OFF
This is ONE TIME OFFER
A confirmation link will be sent to this email address to verify your login. *We value your privacy. We will not rent or sell your email address.
Download Free Demo of VCE Exam Simulator
Experience Avanset VCE Exam Simulator for yourself.
Simply submit your e-mail address below to get started with our interactive software demo of your free trial.