Use VCE Exam Simulator to open VCE files
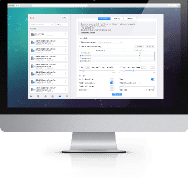
LSSGB Six Sigma Practice Test Questions and Exam Dumps
Question No 1:
The use of station warning lights, tool boards, and jidohka devices in the application of Lean accomplish which of these principles?
A. Pilferage Minimization
B. Visual Factory
C. Management Awareness
D. Operator Attentiveness
Correct answer: B
Explanation:
In Lean manufacturing, the goal is to improve efficiency, reduce waste, and enhance overall productivity. The use of station warning lights, tool boards, and jidohka devices is aimed at creating a more transparent, visual system for both operators and managers to understand the current state of production at a glance. Here's a breakdown of how each tool contributes to Lean principles:
Station warning lights (often called Andon lights) are visual signals used to indicate the status of a workstation or production line. For example, a green light might indicate everything is running smoothly, while a red light could signal a problem or defect that needs immediate attention. This system provides instant visual feedback to everyone in the production area, allowing issues to be addressed quickly and preventing delays.
Tool boards help organize and visually display tools, components, or parts that operators need at their workstations. The purpose of these boards is to ensure that everything is in its place and easy to find, helping reduce downtime and maintain an efficient workflow.
Jidohka devices, part of the autonomation concept, allow machines or operators to stop production automatically when a defect is detected. This principle is critical in Lean because it helps prevent defective products from moving through the production process and ensures quality control at the source.
These practices contribute to the Visual Factory principle in Lean, which emphasizes using visual signals to improve communication, enhance efficiency, and enable quick decision-making. The idea is that visual cues like lights, boards, and devices make it easier for workers and managers to immediately understand the situation and take action, without relying on detailed verbal instructions or complex reports.
Now, let's review the other options:
A. Pilferage Minimization: This refers to reducing theft or unauthorized removal of goods or materials. While Lean practices can help reduce waste and inefficiencies, station warning lights, tool boards, and jidohka devices are not primarily focused on minimizing pilferage.
C. Management Awareness: While these devices certainly make the status of the production process more visible, the main goal is to improve the production process itself rather than solely raising awareness for management.
D. Operator Attentiveness: While these devices do help operators stay aware of their station's status, the primary focus is on creating a visual system that improves overall efficiency, not just keeping operators attentive.
Therefore, the correct principle these tools help achieve is B. Visual Factory, as they all enhance the transparency and visibility of the production environment.
Question No 2:
A Lean Principle that addresses efficiency by the process worker is called ____________________?
A. Visual Factory
B. Supervising
C. Training
D. Standardizing
Correct answer: D
Explanation:
In Lean Manufacturing, the principle that focuses on efficiency by the process worker is known as Standardizing. The concept of standardization ensures that processes are performed in the most efficient and consistent way possible. This involves creating standard operating procedures (SOPs) and best practices that workers can follow to minimize variation and waste, thereby improving overall productivity and quality.
Here’s why the other options are less appropriate:
A. Visual Factory: This refers to the use of visual signals (such as signs, color codes, or displays) in the manufacturing environment to communicate information quickly and clearly to workers. While it helps improve communication and efficiency, it is not directly about the process worker’s efficiency in performing tasks.
B. Supervising: While supervision can help guide workers, it is not a core Lean principle focused on improving efficiency through the worker's process. Lean aims to reduce reliance on supervision by empowering workers and creating standardized processes that workers can follow autonomously.
C. Training: While training is important in Lean to ensure workers have the skills and knowledge to perform tasks efficiently, it is more of a tool for supporting the broader principles of Lean, rather than the Lean principle itself. Training supports standardization but does not directly address it.
Thus, the Lean principle that focuses on efficiency by the process worker is Standardizing, making D the correct answer.
Question No 3:
While management of a company must set the stage for all improvement efforts, which of these 5S's is primarily driven by management?
A. Straighten
B. Sort
C. Shine
D. Sustain
Answer: D
Explanation:
The 5S methodology is a set of principles and practices designed to organize and standardize the workplace to improve efficiency, quality, and safety. The five elements of 5S are: Sort, Set in order (Straighten), Shine, Standardize, and Sustain. While all the elements are essential, Sustain is the one most directly driven by management.
Sort (B) refers to eliminating unnecessary items from the workplace, which is usually initiated at the employee level but requires management support to ensure ongoing focus.
Straighten (A) involves organizing and arranging tools, materials, and equipment so that everything has a place. Again, this is driven by employees, though management must provide the resources.
Shine (C) refers to cleaning and maintaining the work environment, which can be initiated by employees but requires management to allocate resources and encourage the habit.
Sustain (D), however, is the critical element driven by management because it focuses on maintaining the improvements made in the other 4S's over time. Management must establish policies, training programs, and incentives to ensure that 5S practices are sustained long-term.
Sustaining the 5S practices requires consistent reinforcement, monitoring, and management's commitment to embedding these practices into the organizational culture. Thus, Sustain is the 5S that is primarily driven by management.
Question No 4:
As part of a Visual Factory plan __________ cards are created and utilized to identify areas in need of cleaning and organization.
A. Kanban
B. Kaizen
C. Poke-Yoke
D. WhoSai
Correct answer: A
Explanation:
In a Visual Factory plan, Kanban cards are commonly used to help manage workflow and identify areas needing attention, including cleaning and organization. Kanban is a visual scheduling system that uses cards or signals to indicate the status of items or processes. The system helps to visually communicate the need for action, such as restocking materials or cleaning areas.
Here’s why the other options are not correct:
B. Kaizen – Kaizen refers to the practice of continuous improvement through small, incremental changes. While Kaizen is important in the context of workplace organization, it does not specifically involve the use of cards to identify cleaning or organizational needs.
C. Poke-Yoke – Poke-Yoke refers to mistake-proofing mechanisms designed to prevent errors. It focuses on preventing mistakes in the process, rather than organizing or cleaning the factory floor.
D. WhoSai – "WhoSai" does not refer to a recognized methodology or card system related to visual factory planning or organizational practices. This seems to be an incorrect option.
Thus, Kanban cards are the correct tool for identifying areas in need of cleaning and organization within a Visual Factory plan.
Question No 5:
The use of Kanbans work best with pull systems for determining the timing of which products or services are produced.
A. True
B. False
Answer: A
Explanation:
Kanban is a visual signaling system commonly used in lean manufacturing and Agile methodologies to control the flow of work and ensure that production is demand-driven. It is particularly effective when used in pull systems, where products or services are only produced based on actual demand rather than forecasts.
In a pull system, work items (whether they are physical products or services) are only produced or moved through the system when there is a signal that more are needed. This contrasts with a push system, where production happens based on a schedule or forecast, regardless of whether the product is needed.
Kanbans are visual signals (e.g., cards or boards) that indicate when more units are needed, creating a pull of inventory or tasks through the process. The Kanban system helps to maintain an optimal flow by preventing overproduction and reducing waste, which is a key principle of lean manufacturing.
Thus, the statement that Kanbans work best with pull systems is true because Kanbans are designed to regulate and manage the timing and quantity of production based on actual demand, aligning with the principles of a pull system.
Question No 6:
When a Belt applies the practice of Poka-Yoke to a project challenge she is attempting to make certain the activity is _______________ .
A. Well documented
B. Removed from the line
C. Mistake proofed
D. Highly visible
Answer: C
Explanation:
Poka-Yoke is a term derived from Japanese, which translates to "mistake-proofing" or "error-proofing." It is a critical tool used in process improvement methodologies such as Lean and Six Sigma. The primary objective of Poka-Yoke is to design systems, processes, or tasks in such a way that the possibility of human error is either eliminated or minimized to the greatest extent possible. This can be achieved through mechanisms that prevent mistakes from occurring in the first place or that alert the operator when an error is about to happen, ensuring that the quality of the product or process is maintained.
In the context of Lean and Six Sigma, Poka-Yoke is often employed to ensure that the process is "mistake-proofed" (as in C). This could mean designing a process that includes features such as physical constraints, sensors, or alarms that prevent a task from being performed incorrectly. The ultimate goal is to prevent defects, improve quality, and enhance overall process efficiency by ensuring that mistakes do not lead to waste or defects in the final product.
For example, in a manufacturing setting, Poka-Yoke can be used to design machines that automatically stop if an operator places a part incorrectly. Another example could be designing checklists or automated systems that ensure the correct steps are followed in a process. These types of designs reduce the risk of human error, improve the reliability of the output, and save time by preventing the need for rework.
A. Well documented refers to ensuring that procedures are thoroughly written down and followed, but documentation alone does not actively prevent errors. It provides guidance, but it doesn’t inherently stop mistakes from happening.
B. Removed from the line would suggest eliminating the task from the production process entirely, which isn’t aligned with the principles of Poka-Yoke. The focus is more on improving the process to prevent errors rather than eliminating it.
D. Highly visible could be a characteristic of some Poka-Yoke mechanisms (for instance, a flashing light to indicate a mistake), but visibility alone doesn’t ensure that the error will be prevented. The key focus is on error-proofing, not just visibility.
In conclusion, C. Mistake proofed is the correct choice because it directly aligns with the central idea behind Poka-Yoke. The main aim of Poka-Yoke is to design processes and systems in such a way that errors are prevented before they can occur, thereby enhancing overall process efficiency and improving the quality of the final product or service.
Question No 7:
The Lean Principle action in the 5S approach that deals with having those items needed regularly at hand and those items needed less regularly stored out of the way is known as ___________.
A. Shining
B. Standardizing
C. Sustaining
D. Sorting
Answer: D. Sorting
Explanation:
The 5S methodology is a lean management principle aimed at improving efficiency, organization, and cleanliness in the workplace. The name 5S comes from five Japanese words, each representing a key principle: Seiri (Sort), Seiton (Set in order), Seiso (Shine), Seiketsu (Standardize), and Sustain. These principles guide organizations in maintaining a clean and organized workspace that enhances productivity and reduces waste.
Sorting, the first principle of 5S, is the process of identifying and separating necessary items from unnecessary ones. The objective is to eliminate anything that is not required for day-to-day tasks. Items that are essential for daily work should be placed in accessible areas, ensuring that workers can find what they need without wasting time searching. On the other hand, items that are used less frequently or have no immediate value should be stored out of the way, either in storage spaces or removed altogether. By performing the sorting step, organizations create a workspace that is streamlined, less cluttered, and more efficient.
This principle not only improves workspace organization but also helps in identifying inefficiencies and bottlenecks. For example, by observing which tools or supplies are not being used regularly, employees can better evaluate whether those items are necessary for the workflow or if their presence only adds clutter. This step contributes directly to increasing productivity and reducing time spent on unnecessary tasks.
Let’s look at the other 5S principles to understand their relationship:
Shining (Seiso) refers to the cleaning and inspection of the workspace to maintain a tidy environment. This ensures that all tools and equipment are in working order, making the workspace safer and more pleasant.
Standardizing (Seiketsu) ensures that processes for maintaining cleanliness and organization are documented and followed consistently across all areas of the workplace.
Sustaining (Sustain) involves creating habits to ensure that the improvements from the first three S's are maintained over time. This helps create a culture of continuous improvement.
In conclusion, Sorting is the most appropriate Lean Principle in the 5S methodology that focuses on organizing tools, equipment, and materials based on their frequency of use, making it easier for employees to access what they need and improve overall efficiency.
Question No 8:
SPC on the outputs is more preferred than SPC on the inputs when implementing SPC for your process.
A. True
B. False
Answer: A
Explanation:
Statistical Process Control (SPC) is a method used to monitor and control a process through the use of statistical methods. It is designed to identify any variation in the process that could affect the quality of the product or service being produced. By detecting this variation, organizations can take proactive steps to minimize defects and improve product consistency.
In SPC, there are two main areas to consider: inputs and outputs. Inputs refer to the raw materials, resources, or factors that go into a process, while outputs are the final products or results that come from the process. Although monitoring both inputs and outputs is important, SPC on outputs is generally preferred for the following reasons:
Direct Link to Quality:
The primary purpose of SPC is to ensure the quality of the final product or service. By focusing on outputs, the organization is directly monitoring what the customer will receive. This ensures that any deviations from the desired specifications are identified and corrected before the product reaches the customer. In contrast, focusing too much on inputs might not always result in better quality output, as there can be factors in the process that are more influential on the final product than the initial input quality.
Better Control over Process Performance:
Output-based SPC allows for real-time detection of any variations in the final product. If a product starts to deviate from the expected quality, it is easier to pinpoint the root cause of the problem within the process itself. This allows organizations to intervene quickly and adjust the process to correct any inconsistencies. Monitoring inputs might miss this real-time connection, as certain issues might not manifest in the final output until later in the production cycle.
Customer-Centric Focus:
Ultimately, the customer’s experience with the product or service is what matters most. Monitoring outputs ensures that the product delivered meets customer expectations, regardless of whether the inputs were initially correct. The focus on final output ensures that organizations are continually improving the value they provide to the customer.
While monitoring inputs is important for process design and stability, output-based SPC gives organizations a clearer and more immediate indication of whether their processes are delivering the expected quality. This leads to more timely corrective actions, reduced defects, and a greater ability to maintain consistent product quality.
Therefore, the statement that SPC on outputs is more preferred than SPC on inputs when implementing SPC is correct. The primary goal of SPC is to ensure the product meets the quality standards expected by the customer, and output-focused SPC directly supports this goal.
Question No 9:
Significant variation in process performance is a consequence of several causes that can be classified using which of the terminologies shown. (Note: There are 2 correct answers).
A. Common
B. Random
C. Uneducated
D. Special
E. Vital
Answer: A and D
Explanation:
In quality management and process control, variation in process performance can be categorized into two primary types based on its origin:
Common Cause Variation (A):
This type of variation, also called systematic variation, is inherent in the process and is always present in the system. It reflects the normal or baseline variability in the process and is typically caused by factors such as machine wear, environmental factors, or standard operating procedures. Common cause variation is the expected, usual variation within the system, and efforts to reduce it would focus on improving the overall process.
Special Cause Variation (D):
This type of variation is caused by specific, identifiable factors that are not part of the normal process. It can be the result of unexpected events such as equipment malfunction, human error, or external disruptions. Special cause variation is often sporadic and does not occur continuously. Identifying and addressing these causes is crucial for improving process stability.
Let’s break down why the other options are incorrect:
B. Random:
While some variability might seem random, this term is not typically used in the context of classifying causes of variation in process performance. "Random" is more of an explanation of variability, not a classification like common or special causes.
C. Uneducated:
This is not a recognized term in the context of process variation classification. It doesn’t apply to quality control or process improvement terminology.
E. Vital:
This term is also not related to process variation classification. It might be used in other contexts, such as identifying essential factors, but not in the context of process variability.
Therefore, the correct answers are A (Common) and D (Special), as they represent the two primary types of causes for variation in process performance.
Question No 10:
When it comes to Control, one of the most effective means of eliminating defects is to _________________ .
A. Train personnel often and thoroughly
B. Keep a Six Sigma project going on the process at all times
C. Design defect prevention into the product
D. Have each process consist of no more than five steps
Answer: C
Explanation:
In the context of the Six Sigma methodology, the Control phase is all about maintaining the gains achieved during the improvement phases and ensuring that defects are consistently prevented over time. One of the most effective ways to eliminate defects is to design defect prevention into the product from the outset. This approach is rooted in the principle of built-in quality, which aims to prevent defects rather than merely detecting and fixing them after they occur. By integrating quality measures into the design and development processes, organizations can reduce the likelihood of defects arising, ensuring that the final product consistently meets the desired standards.
A. Train personnel often and thoroughly is important for ensuring that employees understand and adhere to quality standards. However, training alone cannot prevent defects unless it is integrated with other quality control processes.
B. Keep a Six Sigma project going on the process at all times may be beneficial for ongoing process improvement, but it is not a direct method of preventing defects during the Control phase.
D. Have each process consist of no more than five steps could be part of a simplification strategy, but it does not directly address defect prevention in a comprehensive way. While reducing complexity may help, it is not the primary method for eliminating defects.
Therefore, the most effective approach to eliminating defects in the Control phase is C. Design defect prevention into the product.
Top Training Courses
SPECIAL OFFER: GET 10% OFF
This is ONE TIME OFFER
A confirmation link will be sent to this email address to verify your login. *We value your privacy. We will not rent or sell your email address.
Download Free Demo of VCE Exam Simulator
Experience Avanset VCE Exam Simulator for yourself.
Simply submit your e-mail address below to get started with our interactive software demo of your free trial.