Use VCE Exam Simulator to open VCE files
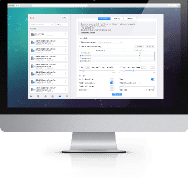
MB-330 Microsoft Practice Test Questions and Exam Dumps
You are in the process of setting up Dynamics 365 Supply Chain Management for a client. The client plans to add multiple items to the system and needs to configure them based on ownership. Specifically, the client wants to have the option to classify items as either company-owned or consignment when creating these items.
Which two actions should you take to allow the client to configure items as company-owned or consignment during item creation in Dynamics 365 Supply Chain Management?
(Note: Each correct answer is worth one point.)
A. Enable batch dimension.
B. Enable owner dimension.
C. Allocate a moving average costing inventory model.
D. Allocate a standard costing inventory model.
To meet the requirement of classifying items as company-owned or consignment in Dynamics 365 Supply Chain Management, certain configuration settings must be enabled. Let's break down the two necessary steps:
B. Enable Owner Dimension
The Owner dimension is key when you need to track ownership of inventory. In Dynamics 365 Supply Chain Management, enabling this dimension allows you to distinguish between items that are company-owned and those that are on consignment. The Owner dimension essentially adds an additional layer of classification to inventory items, allowing the system to separate stock based on ownership, which is exactly what the client needs. This enables easy tracking and management of items that belong to the company versus those that are held on consignment.
C. Allocate a Moving Average Costing Inventory Model
The Moving Average costing model is useful when you need to track the cost of items that fluctuate in price over time. In scenarios where the client is dealing with consignment items, where costs might vary based on agreements with external suppliers, the moving average model will allow for a flexible costing method. This model helps the system maintain an average cost for items as they are used or sold. This aligns well with consignment items because consignment stock often has different cost structures compared to company-owned inventory. By using the moving average costing model, the client can more accurately manage the costs of both company-owned and consignment items.
A. Enable Batch Dimension
The batch dimension is typically used when tracking inventory that is organized into batches, such as pharmaceutical products or food items that need batch tracking. While it’s important in certain industries, it doesn’t directly relate to tracking ownership of items. Thus, enabling the batch dimension is not necessary for distinguishing between company-owned and consignment items.
D. Allocate a Standard Costing Inventory Model
The standard costing model is used for items where a fixed cost is predetermined for each unit. It’s more useful for organizations with predictable pricing for their goods. However, for consignment items, where costs can fluctuate based on the supplier's terms, the standard costing model is less appropriate. In this case, the moving average costing model provides the necessary flexibility.
To meet the client’s needs for classifying items as company-owned or consignment, you should enable the owner dimension (B) to track ownership and allocate a moving average costing inventory model (C) to accurately manage the fluctuating costs of these items.
Your company uses Dynamics 365 Supply Chain Management for managing customer purchase agreements. You are tasked with configuring a purchase agreement that provides clients with specific unit discounts based on the quantity purchased. The discount tiers are as follows:
A 10% discount per unit for purchases between 51 and 100 units
A 15% discount per unit for purchases of 101 units or more
You configure a purchase agreement to reflect these discount conditions.
Does the configuration of the purchase agreement achieve the objective of applying the specified discounts based on the quantity purchased?
A. Yes, it does
B. No, it does not
In Dynamics 365 Supply Chain Management, configuring purchase agreements to offer discounts based on the quantity of items purchased requires precise configuration. However, the given scenario likely will not achieve the desired outcome as stated in the question. Here's why:
Understanding Purchase Agreement Discounts in Dynamics 365 SCM
Purchase agreements in Dynamics 365 Supply Chain Management allow you to define discount structures, but these agreements are typically based on cumulative quantities or value-based discounts. However, for quantity-based discounts to be applied correctly, the discount terms need to be structured with the correct conditions.
Issue with Current Configuration
Based on the description of the discount tiers in the question, it seems that two distinct discount levels (10% for 51-100 units and 15% for 101+ units) should be applied based on quantity breaks. While purchase agreements can certainly include quantity-based discount terms, the way they are configured in the question does not appear to specify these quantity breaks clearly. In order to achieve the desired outcome, line discounts or volume-based discount structures should be configured based on these specific thresholds.
In Dynamics 365, you would typically need to set up a line discount or trade agreement with conditions that specify the quantity ranges (51-100 and 101+) and the associated discounts (10% and 15% per unit). Without correctly configuring these conditions, the system may not recognize or apply the correct discount rates based on the quantities ordered by the customer.
Correct Configuration Approach
To achieve the desired result, you would need to:
Create a trade agreement with the item and vendor.
Set up quantity-based discount conditions for the appropriate quantity ranges.
Define the discount percentage that applies for each range (10% for 51-100 and 15% for 101+).
Without explicitly setting these conditions in the system, the purchase agreement may not function as expected, and the discount will not be applied correctly.
To ensure that the 10% and 15% unit discounts are applied correctly based on the quantity purchased, the purchase agreement must be configured with specific quantity-based discount conditions. Therefore, the configuration as described in the question does not achieve the objective.
Your company uses Dynamics 365 Supply Chain Management to manage customer transactions. You are tasked with configuring a trade agreement that offers clients specific discounts based on the quantity of a particular item they purchase. The discount parameters are as follows:
10% discount per unit when purchasing between 51 and 100 units
15% discount per unit when purchasing 101 or more units
You proceed to configure a trade agreement to reflect these discount conditions.
Does the configuration of the trade agreement correctly achieve the objective of applying the specified discounts based on the quantity of items purchased?
A. Yes, it does
B. No, it does not
In Dynamics 365 Supply Chain Management, trade agreements are used to define special pricing and discount rules for customers based on various conditions, including quantity. The task here is to configure the trade agreement to apply a unit-based discount depending on the quantity purchased. Let’s break down how the trade agreement setup can accomplish this:
Understanding the Trade Agreement Setup: Trade agreements in Dynamics 365 SCM can be configured to offer quantity-based discounts. These agreements allow businesses to specify the conditions under which certain discounts apply, such as the quantity range (e.g., 51-100 units, 101+ units) and the discount percentage for those ranges (e.g., 10% and 15% per unit).
Configuration Steps to Achieve the Objective: To achieve the discount structure described, you need to configure the trade agreement with the following:
Set up quantity-based discount terms that apply specific discounts based on the quantity thresholds. In this case, you would define:
10% discount for orders between 51 and 100 units.
15% discount for orders of 101 units or more.
Trade agreement types should be defined appropriately, either for customers or items, so that the system knows which specific agreements to apply.
You also need to configure the line discount settings to ensure that the discount is applied per unit, as required by the parameters of the question.
Validation and Outcome: After configuring the trade agreement with the quantity-based discount conditions, the system will automatically apply the 10% discount when the quantity is between 51 and 100 units and the 15% discount when the quantity is 101 units or more. This ensures that the trade agreement is in line with the specified requirements of offering discounts per unit based on the order quantity.
Why This Meets the Objective: The trade agreement configuration is the appropriate solution because it allows you to specify quantity tiers and the corresponding discounts per unit. The system will apply these conditions during the transaction process, ensuring the correct discount is applied based on the client’s order quantity.
The configuration of the trade agreement with quantity-based discount terms will indeed achieve the objective of applying the correct unit discounts based on the quantity purchased. Therefore, the correct answer is A. Yes, it does.
Your company has recently implemented Dynamics 365 Supply Chain Management to manage inventory. You are in the process of configuring costing methods for the items in your inventory. Some of these items have a limited shelf life, and you need to select the appropriate costing method to ensure the correct inventory valuation.
Which costing method should you use for items with a limited shelf life in Dynamics 365 Supply Chain Management?
A. Standard
B. FIFO
C. Average
D. Specific
In Dynamics 365 Supply Chain Management, choosing the right costing method is crucial to managing inventory accurately, especially when dealing with items that have a limited shelf life, such as perishable goods, pharmaceuticals, or food items. These items require specific inventory valuation methods to ensure that the oldest stock is used or sold first to prevent wastage and reduce the risk of expired products being sold.
Let's break down the different costing methods and identify why FIFO is the best choice for items with a limited shelf life:
FIFO (First In, First Out):
FIFO is the preferred costing method for items with a limited shelf life because it ensures that the oldest inventory (first in) is sold or used first (first out).
This method works well with products that have an expiration date, as it guarantees that older items are used before newer ones, thus minimizing the risk of products expiring while still in inventory.
In Dynamics 365 SCM, the FIFO method allows the system to track the movement of stock, ensuring that the inventory valuation reflects the cost of the oldest items first, which aligns with the physical movement of goods in a warehouse.
Standard Costing:
Standard costing involves assigning a fixed cost to each item, regardless of its actual purchase price. While this method is suitable for items with stable prices, it is not ideal for items with a limited shelf life, as it does not account for variations in purchase costs or the expiration of inventory.
Therefore, it is not the best choice for perishable or time-sensitive goods.
Average Costing:
Average costing calculates the average cost of items in inventory, taking into account both old and new stock. This method is useful when the inventory is homogeneous or when precise tracking of item age is not required.
However, it does not prioritize the oldest inventory, so it is not the most appropriate method for managing perishable items.
Specific Identification:
The Specific costing method is used when each individual item is tracked by its specific cost, such as with luxury goods or high-value items.
This method is not as efficient for managing bulk items with expiration dates, as it requires detailed tracking of each unit, which can be cumbersome for items with a limited shelf life.
For items with a limited shelf life, the FIFO (First In, First Out) method is the most appropriate costing method because it ensures that older items are used or sold first, minimizing the risk of wastage and expired inventory. Therefore, the correct answer is B. FIFO.
Your company operates multiple distribution warehouses across the USA, and you are responsible for configuring the barcode system in Dynamics 365 Supply Chain Management. The goal is to enable the use of barcodes in order to automate the scanning process for inventory management across the warehouses.
You need to configure barcode scanning so that barcodes are automatically entered when scanned, facilitating seamless inventory tracking and operations.
How should you configure the system in Dynamics 365 Supply Chain Management to enable the automatic entry of barcodes during scanning across your distribution warehouses?
To achieve this goal, follow the steps below to configure barcode scanning in Dynamics 365 Supply Chain Management:
Navigate to the Warehouse Management Module:
In Dynamics 365 SCM, barcode scanning is typically configured within the Warehouse Management module, which governs all logistics and warehouse operations. Go to Warehouse Management from the main menu.
Setup Barcode Scanning:
Once in the Warehouse Management module, navigate to Setup > Mobile Devices > Mobile Device Configuration.
This is where you configure different mobile device profiles and set up scanning functionality for the warehouse operations.
Configure Mobile Device Profiles:
Define a Mobile Device Profile for your warehouse operations. This profile includes configurations for how barcodes will be scanned and processed.
You will need to set up the device types and ensure the barcode formats (e.g., Code 128, Code 39, or QR codes) are supported by the system.
Configure the scanning functionality to ensure that once the barcode is scanned, the relevant item or inventory record is automatically updated in the system.
Integrate with Warehouse Workflows:
Link the barcode scanning functionality with your warehouse workflows. This can include receiving, picking, shipping, and inventory management.
Ensure that when items are scanned, the barcode data automatically populates the appropriate fields in the system, such as item numbers, lot numbers, or serial numbers.
Testing and Deployment:
After configuring the barcode scanning, it’s essential to test the setup in a staging or test warehouse to ensure that the barcodes are being automatically read and entered into the system without errors.
Once confirmed, deploy the solution across all your distribution warehouses.
In Dynamics 365 Supply Chain Management, configuring barcode scanning allows for seamless automation of inventory and warehouse operations, especially in distribution centers. Barcodes can be scanned to quickly update inventory records, facilitating faster and more accurate order processing, stock-taking, and product tracking.
Barcode scanning helps reduce manual data entry errors, speeding up warehouse processes such as receiving, picking, and shipping items.
It ensures accuracy in inventory tracking, allowing the system to record precise quantities and item locations.
Warehouse Management Module: The first step is to go to the Warehouse Management module, which is where all logistics and inventory management tasks are configured. This module is specifically designed to support the scanning of barcodes and the integration of mobile devices used by warehouse workers.
Mobile Device Profiles: The system allows you to create different mobile device profiles, each with specific configurations for barcode scanning. This includes setting up the type of device used (e.g., handheld barcode scanners, mobile terminals) and ensuring compatibility with the barcode formats in use at your company.
Linking to Warehouse Processes: The barcode scanning should be linked to specific warehouse operations such as receiving, picking, and shipping. By doing this, any barcode scan will automatically update the relevant system records, such as inventory counts, lot numbers, or location information, which significantly reduces manual effort.
Testing: Before rolling out the configuration across all distribution warehouses, thorough testing in a controlled environment ensures that the barcode scans are being correctly interpreted and processed by the system.
The configuration of barcode scanning in Dynamics 365 Supply Chain Management involves setting up mobile device profiles, ensuring proper integration with warehouse workflows, and testing the functionality before deployment. This setup streamlines warehouse operations and enhances inventory accuracy, making it a crucial feature for businesses with multiple distribution warehouses.
Your company is in the process of testing a new implementation of the Dynamics 365 Supply Chain Management procurement module. During testing, you notice that when items are received, transactions are not being posted to the product receipt journal. You need to resolve this issue to ensure that transactions are recorded correctly.
Which of the following actions should you take in the Item model group setup form to resolve this issue?
A. Uncheck the Include physical value checkbox.
B. Check the Include physical value checkbox.
C. Uncheck the Accrue liability on product receipt checkbox.
D. Check the Accrue liability on product receipt checkbox.
In Dynamics 365 Supply Chain Management, the Item model group setup plays a key role in determining how inventory transactions are posted when items are received, sold, or moved within the system. If you're not seeing transactions being posted to the product receipt journal, it’s likely that a critical configuration is missing or incorrectly set.
The Item model group defines how inventory transactions are processed. It determines if inventory and financial transactions are posted at the time of receipt, issue, or sales. One of the key options related to the posting of transactions during product receipt is the Accrue liability on product receipt option.
When the Accrue liability on product receipt option is enabled, liabilities for the items received are automatically recognized in the system when the products are received. This allows the product receipt journal to capture the necessary financial entries and helps ensure that liabilities are properly recorded at the time of receipt, even before the invoice is posted.
When this checkbox is unchecked, the liability is not accrued at the time of product receipt. This can result in the absence of financial postings in the product receipt journal, as the system will wait until the invoice is posted before recognizing the liability.
When this checkbox is checked, liabilities are recognized when the items are received, ensuring that the system generates the appropriate journal entries for the product receipt, thus posting the transactions correctly.
A. Uncheck the Include physical value checkbox:
The Include physical value checkbox determines whether physical inventory value is included in the transactions, but it does not directly affect the posting of transactions to the product receipt journal.
B. Check the Include physical value checkbox:
This action would affect how inventory value is treated in financial transactions, but it does not resolve the issue of transactions not being posted to the product receipt journal.
C. Uncheck the Accrue liability on product receipt checkbox:
Unchecking this would prevent liabilities from being recognized when products are received, which is the opposite of what is needed to ensure proper posting of transactions in the product receipt journal.
The correct solution to ensure that transactions are posted to the product receipt journal when items are received is to check the Accrue liability on product receipt checkbox. This ensures that liabilities are automatically recognized at the time of product receipt, triggering the appropriate transactions in the journal.
A manufacturing company is using the Dynamics 365 Supply Chain Management system to streamline its processes. As part of their setup, they make use of Bill of Materials (BOM) templates to speed up the creation of BOMs for various items and service objects.
You need to determine the correct statements regarding the use of BOM templates within the system.
Which of the following statements are TRUE regarding BOM templates in Dynamics 365 Supply Chain Management? (Select all that apply.)
A. You can only apply a single template BOM to a service object.
B. You can apply many template BOMs to a service object.
C. You can modify or delete lines in a BOM template regardless of whether the template has been associated with a service object or not.
D. You can modify or delete lines in a BOM template as long as the template has not been associated with a service object.
In Dynamics 365 Supply Chain Management, the use of Bill of Materials (BOM) templates is an important way to streamline the process of creating BOMs for various products, assemblies, and service objects. By using templates, businesses can quickly apply standard materials and components to new BOMs without having to manually configure each one from scratch.
Application of Multiple BOM Templates:
Option B: You can apply many template BOMs to a service object.
This statement is TRUE. In Dynamics 365, it’s possible to apply multiple BOM templates to a single service object. This flexibility allows you to combine the contents of different templates to better suit the requirements of the service object. This is particularly useful when multiple types of materials or components are required for different purposes or when the service object involves complex configurations.
Single Template BOM Application:
Option A: You can only apply a single template BOM to a service object.
This statement is FALSE. As explained in Option B, multiple template BOMs can be applied to a service object. This flexibility allows for more complex and detailed BOM structures when required.
Modification of BOM Template Lines:
Option C: You can modify or delete lines in a BOM template regardless of whether the template has been associated with a service object or not.
This statement is FALSE. Once a BOM template is associated with a service object, certain modifications may be restricted depending on the setup and permissions. In Dynamics 365, templates are designed for reuse and consistency. Modifications may be limited if the template has already been applied to a service object to avoid unintentional disruptions.
Modification of BOM Template Lines Before Association:
Option D: You can modify or delete lines in a BOM template as long as the template has not been associated with a service object.
This statement is TRUE. Before a BOM template is applied to a service object, you are free to modify or delete any lines within the template. This flexibility allows you to update the BOM template as needed before it is assigned, ensuring that the correct materials and components are included.
The correct answers are B and D. BOM templates in Dynamics 365 Supply Chain Management provide significant flexibility, but it’s important to understand how the association with service objects impacts the ability to modify and apply them. You can apply multiple templates to a service object, and modifications to a template can be made as long as it has not yet been associated with a service object.
Your company is using Dynamics 365 Supply Chain Management for its warehouse operations. After implementing warehouse locations, you have been tasked with configuring location directives to optimize inventory movement. Specifically, you need to create a location directive that can help with the identification of similar items in the warehouse for efficient movement.
Which of the following strategies should you use in your location directive to ensure the identification of similar items in the warehouse?
A. Match packing quantity
B. Location aging FIFO
C. Location aging LIFO
D. Consolidate
In Dynamics 365 Supply Chain Management, location directives are used to define the rules for managing inventory movements within the warehouse. These directives guide the system in determining how inventory is handled when it is picked, put away, or moved, based on defined criteria. One of the critical tasks when configuring location directives is to ensure that items are identified correctly and efficiently in the warehouse.
A. Match packing quantity:
This strategy ensures that items with matching packing quantities are grouped together during inventory handling. However, it does not focus on identifying similar items based on other factors like item types, locations, or categorization. While useful for packaging consistency, it is not the most effective option for identifying similar items in the warehouse.
B. Location aging FIFO (First In, First Out):
FIFO is a method used to manage inventory based on the age of the items, ensuring that the oldest inventory is used first. While this is an essential strategy for managing stock rotation and freshness (particularly for perishable items), it does not directly relate to identifying similar items in the warehouse. FIFO is more concerned with stock age rather than item similarity.
C. Location aging LIFO (Last In, First Out):
LIFO is another method for inventory management, which focuses on using the most recently received items first. Like FIFO, this strategy manages the movement of inventory based on the receipt date rather than item characteristics. While it’s useful in specific scenarios (such as when market prices fluctuate), it is not designed to identify similar items.
D. Consolidate:
Consolidate is the correct strategy to use when you want to identify similar items in the warehouse. This strategy helps the system group items with similar characteristics or from the same category together in a consolidated location. By using this directive, the system can efficiently manage similar items in one area, optimizing inventory handling and improving storage space utilization. This is particularly useful when managing items that need to be identified and moved together based on shared attributes.
The Consolidate strategy allows the warehouse system to group similar items, based on defined attributes, for easier inventory management and efficient movement. This helps streamline operations by reducing the time and complexity of managing different items spread across various locations.
The correct strategy for identifying similar items in the warehouse is D. Consolidate. This directive groups items with shared characteristics in the same location, optimizing the process of handling and moving similar inventory in the warehouse.
Top Training Courses
SPECIAL OFFER: GET 10% OFF
This is ONE TIME OFFER
A confirmation link will be sent to this email address to verify your login. *We value your privacy. We will not rent or sell your email address.
Download Free Demo of VCE Exam Simulator
Experience Avanset VCE Exam Simulator for yourself.
Simply submit your e-mail address below to get started with our interactive software demo of your free trial.