Use VCE Exam Simulator to open VCE files
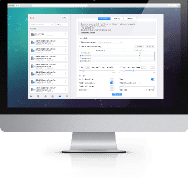
CQA ASQ Practice Test Questions and Exam Dumps
Question No 1:
What is the definition of a root cause of a nonconformance?
A. is discovered by conducting designed experiments
B. is established through the use of fishbone diagrams
C. must be reviewed by the material review board
D. must be corrected in order to prevent a recurrence
Correct Answer: D
Explanation:
In quality management, identifying and addressing the root cause of a nonconformance is critical to ensuring that the issue does not recur. The root cause is the fundamental issue or underlying factor that leads to the occurrence of the nonconformance. To prevent future occurrences of the same issue, it is essential that the root cause is addressed effectively.
The correct answer, D, highlights that a root cause must be corrected in order to prevent a recurrence. This is the key to successful quality control and continuous improvement processes. Simply addressing symptoms or treating the issue superficially without targeting the root cause will likely result in the problem recurring. The corrective actions that result from identifying the root cause are aimed at eliminating it, thereby preventing the same nonconformance from happening again.
Let’s consider the other options and why they are not as suitable in defining the root cause:
A: "is discovered by conducting designed experiments" – While designed experiments can help identify potential causes of nonconformance or variations in a process, they do not necessarily define a root cause. Root causes often require a more comprehensive approach that may involve multiple tools or techniques. It’s not just about discovering a problem; it’s about understanding and addressing its underlying cause.
B: "is established through the use of fishbone diagrams" – Fishbone diagrams (also known as Ishikawa or cause-and-effect diagrams) are a helpful tool in identifying potential causes of a problem. However, a root cause is not automatically established through this technique. The fishbone diagram is just one step in the problem-solving process, and it may require further analysis and investigation to pinpoint the true root cause. While it helps visualize and categorize causes, it does not guarantee that the root cause will be identified unless further investigation is conducted.
C: "must be reviewed by the material review board" – While the Material Review Board (MRB) is typically involved in decisions regarding materials, parts, or products that do not conform to specifications, the review by the MRB is not a defining characteristic of a root cause. The MRB’s role is more focused on managing nonconforming items rather than directly identifying or correcting root causes.
To sum up, the root cause of a nonconformance is an underlying issue that must be addressed to prevent future occurrences, which is best captured by answer D.
Question No 2:
What is the term for the comparison of lower-tier documents to higher-tier documents before fieldwork begins?
A. desk audit
B. process audit
C. conformance audit
D. management audit
Correct answer: A
Explanation:
Before starting fieldwork in auditing or project management, comparing lower-tier documents (e.g., detailed reports, records, or data) with higher-tier documents (e.g., strategic plans, policies, or overall project guidelines) is a critical step. This process helps ensure alignment and accuracy between the different levels of documentation and identifies potential issues early on. This type of comparison is known as a desk audit.
A desk audit involves reviewing documents and records without physically inspecting or observing operations on-site. It is typically performed to verify the consistency, accuracy, and appropriateness of records against higher-level requirements or objectives. During a desk audit, auditors will examine documents such as financial statements, project plans, contracts, or compliance reports to ensure that they align with regulatory standards, organizational goals, or other authoritative criteria.
Now, let’s explore the other options:
B. A process audit focuses on examining and assessing the procedures or processes used in an organization, rather than comparing documents. It looks at how tasks are performed to ensure efficiency, compliance, and effectiveness. While it might occur during fieldwork or as part of a larger audit, it is not the specific term for comparing lower-tier documents to higher-tier documents.
C. A conformance audit is an audit type that checks if an organization's activities, processes, or products comply with a set of standards, regulations, or specifications. While a desk audit could be part of a conformance audit, conformance auditing broadly focuses on verifying compliance with rules, rather than merely comparing documents at different levels before fieldwork.
D. A management audit evaluates the efficiency and effectiveness of an organization's management, including its policies, procedures, and organizational structure. It is broader in scope and focuses more on managerial effectiveness rather than comparing documents before the fieldwork begins.
In conclusion, the comparison of lower-tier documents to higher-tier documents before fieldwork starts is a desk audit. It helps ensure that all necessary documentation is aligned and correct before more detailed examination or investigation takes place during the actual fieldwork phase.
Question No 3:
Why is an audit trail necessary?
A. Schedule and budget for audit assignments
B. Show how and when items were reviewed
C. Provide management with justification for an audit
D. Provide the audit manager with audit results
Correct answer: B
Explanation:
An audit trail is a chronological record that provides a detailed history of the processes, transactions, or activities during an audit. The primary purpose of an audit trail is to show how and when items were reviewed (option B). It tracks the steps, decisions, and actions taken throughout the auditing process, which is critical for transparency and accountability. This trail helps auditors and other stakeholders understand how conclusions were reached and which sources of information were used at each stage of the audit. In other words, the audit trail serves as a documented history of the audit, ensuring that all procedures and findings are traceable.
Having an audit trail is essential for establishing credibility and for verifying that the audit process has been conducted appropriately and thoroughly. It also ensures that any steps taken in the audit process can be reviewed or revisited if necessary, providing evidence of how conclusions were formed.
Option A refers to scheduling and budgeting audit assignments, which is part of audit planning but is not directly tied to the purpose of an audit trail. An audit trail is not about organizing or managing resources for the audit, but rather about documenting the audit process.
Option C addresses providing management with justification for an audit. While an audit trail may indirectly help to demonstrate the integrity and thoroughness of an audit, its primary role is not to justify the audit but to track and record the audit activities. Justification for an audit is generally established through initial planning and agreement on the scope and objectives of the audit.
Option D refers to providing the audit manager with audit results, which is a function of the audit report, not the audit trail. The audit trail doesn't provide the final audit results, but rather records the actions and decisions taken during the audit process, leading up to the results.
In conclusion, an audit trail's primary function is to show how and when items were reviewed, ensuring transparency and accountability throughout the auditing process. This record helps ensure that the audit can be revisited or reviewed for accuracy and compliance, making it a critical component of the audit process.
Question No 4:
Which audit strategy is commonly used to assess compliance to a specific requirement across all locations where that requirement is applicable?
A. Discovery method
B. Element method
C. Department method
D. Process method
Answer: D
Explanation:
When conducting an audit to assess compliance to a specific requirement, especially across multiple locations, it is essential to use an approach that can effectively evaluate the same requirement in varied contexts. The process method is the most suitable approach in this case because it focuses on auditing the specific processes that are in place to ensure compliance. This strategy evaluates the implementation of particular processes that apply to the requirement at each location, regardless of differences in the local environment. By auditing the processes, the organization can verify whether the same standards and requirements are being met consistently across all sites.
In option A, the discovery method is typically more exploratory and used for initial investigations or to uncover unknown issues. It is not as structured or targeted for assessing ongoing compliance with a specific requirement across locations. This method is better suited for identifying potential risks or areas of non-compliance but is not a common strategy for regular auditing against established standards.
Option B refers to the element method, which might involve auditing specific elements or components of a system or process. While this method could be useful for assessing certain individual factors, it doesn’t inherently focus on assessing compliance across multiple locations in a holistic manner, which makes it less appropriate for the given scenario.
Option C mentions the department method, which would typically focus on auditing compliance within specific departments. While this method can be effective for assessing how a requirement is implemented within a particular functional area, it may not comprehensively address compliance across all locations unless the departments span multiple sites. It is not as broadly applicable to locations as the process method.
The process method stands out because it provides a comprehensive and structured approach to ensuring that a specific requirement is followed uniformly across various locations. It focuses on the consistency and effectiveness of processes that are responsible for achieving compliance, making it the most effective and common strategy for this type of audit.
Thus, the correct answer is D.
Question No 5:
What conclusion can an auditor make if they observe that statistical process control (SPC) charts near operator workstations are done correctly and are regularly completed throughout the plant?
A. Commitment of management to quality is strong
B. Processes are being improved continually
C. Shop floor staff have been fully trained
D. SPC charts are available
Correct Answer: D
Explanation:
When an auditor observes that SPC charts are posted correctly and regularly completed throughout a plant, they are witnessing a form of process monitoring and data recording. However, this observation alone does not provide conclusive evidence regarding broader aspects such as management commitment, process improvement, or staff training.
Option A suggests that the commitment of management to quality is strong based on the correct use and completion of SPC charts. While it's possible that management supports the use of SPC as a quality tool, the auditor cannot definitively conclude the strength of management’s overall commitment to quality just from this observation. Management commitment goes beyond ensuring that charts are used; it encompasses how actively management participates in quality initiatives, allocates resources for quality improvement, and fosters a culture of quality throughout the organization. Simply having SPC charts posted doesn’t guarantee that these deeper aspects of quality management are effectively in place.
Option B suggests that processes are being improved continually. While SPC charts provide data on process variation, their mere presence and regular completion do not confirm whether the data is being actively analyzed and used to drive improvements. For continual improvement to occur, the data from SPC charts must be systematically reviewed, action plans must be developed based on this data, and corrective measures should be taken when necessary. The auditor cannot draw conclusions about the continuous improvement process based solely on the observation of SPC chart usage.
Option C suggests that shop floor staff have been fully trained. While it is likely that the correct and regular use of SPC charts indicates some level of training, the auditor cannot definitively conclude that all shop floor staff have been fully trained just by observing the charts. The use of SPC charts is a tool, and the skill level of staff should be assessed through more direct indicators, such as training records, assessment of staff competencies, or observations of their ability to analyze and respond to the data presented by SPC charts.
Option D is the most accurate conclusion. The auditor is simply observing that SPC charts are present and are being completed regularly, which indicates that the tool for monitoring process variation is available. The fact that these charts are posted and correctly filled out shows that the data collection system is in place and being utilized. However, this observation doesn’t provide insight into how the data is being used, whether corrective actions are being taken, or whether staff are fully trained to interpret and act on the charts.
In summary, the auditor can conclude that the SPC charts are available and being used consistently, but they cannot make inferences about broader quality management processes, management commitment, or staff training from this observation alone.
Question No 6:
Under what circumstances is it appropriate to allow an extension for the time frame of a corrective action?
A. When the auditor cannot perform the follow-up audit as scheduled
B. When the auditee determines that the proposed corrective action is not cost-effective
C. When the corrective action plan requires more time than originally anticipated
D. When there has been a change in operators who perform the task
Answer: C
Explanation:
Corrective actions are taken to address deficiencies or non-conformities identified during audits or assessments. These actions are typically accompanied by a timeline for completion to ensure that the issues are resolved promptly. However, there are times when it may be necessary to extend the time frame for a corrective action.
The most valid reason for granting an extension of the time frame is when the corrective action plan requires more time than originally anticipated. This can occur for a variety of reasons, such as unexpected complexities in implementing the corrective measures, resource limitations, or the need for additional planning or testing. In such cases, it’s important to evaluate whether the corrective action is being properly executed and whether the timeline needs to be adjusted to ensure the solution is effective. Therefore, the correct choice is C. An extension is warranted if more time is needed to fully implement the corrective action, as long as the reasoning is justified and the extended time does not compromise the overall objective of resolving the issue.
Now, let's examine the other options:
A. When the auditor cannot perform the follow-up audit as scheduled — This is not a valid reason to extend the time frame for a corrective action. The corrective action itself should be evaluated independently of the auditor's availability. Auditors may need to reschedule their audits, but this does not directly affect the timeline of implementing the corrective action itself.
B. When the auditee determines that the proposed corrective action is not cost-effective — While cost considerations are important, the decision to extend a corrective action timeline is not typically based on the cost-effectiveness of the action itself. If a corrective action is deemed too costly, the auditee might look for alternative actions or solutions, but this does not automatically justify extending the time frame. Cost-effectiveness might influence the corrective action's approach but not the extension of the timeline for implementing it.
D. When there has been a change in operators who perform the task — A change in operators could potentially affect the effectiveness of the corrective action, especially if the new operators require training or additional time to become familiar with the process. However, this reason alone may not justify an extension. If training or knowledge transfer is needed, it may be considered as part of the corrective action but would need to be appropriately planned rather than causing a blanket extension of the timeline.
In conclusion, the only circumstance in which it is directly acceptable to grant an extension of the time frame is C, when the corrective action plan requires more time than originally anticipated. This ensures that the corrective action is given the necessary time to be fully and effectively implemented.
Question No 7:
Which type of control chart is used to plot the fraction of nonconforming products?
A. p chart
B. u chart
C. np chart
D. c chart
Answer: A
Explanation:
Control charts are statistical tools used in quality control to monitor the stability and variation of processes over time. They help identify whether a process is operating within acceptable limits or whether adjustments need to be made. Different types of control charts are used depending on the type of data being monitored and the process characteristics.
When considering the fraction of nonconforming products in a batch, the p chart is the appropriate tool. The p chart (proportion chart) is used to track the proportion of defective items in a sample or batch, where the data is expressed as a fraction or percentage. This is ideal for situations where the product being analyzed is either "conforming" or "nonconforming," and the chart monitors the variability in the proportion of nonconforming products over time. The p chart is designed for scenarios where sample sizes can vary, and it provides insight into whether the proportion of nonconforming items is stable or changing beyond acceptable limits.
In contrast, the other options do not serve the same purpose:
B. u chart: The u chart is used to monitor the number of defects per unit when the sample size is variable. It tracks the average number of defects in a unit, not the fraction of nonconforming products.
C. np chart: The np chart tracks the number of nonconforming items in a sample, but it assumes the sample size is constant. It counts the number of defective items rather than focusing on their proportion. This can be useful when sample sizes do not change and you are more interested in the raw count of defects.
D. c chart: The c chart is used to monitor the number of defects in a fixed sample size or unit. It counts the total number of defects (not defective units) per sample, which differs from tracking the fraction of nonconforming products.
In conclusion, when you are tracking the fraction of nonconforming products, the most appropriate control chart to use is the p chart, making A the correct answer. It allows you to monitor the proportion of defective items over time, ensuring that process performance stays within desired control limits.
Question No 8:
How can auditors utilize flowcharts in their auditing process?
A. Analyze the causal factors of process dispersion
B. Understand the overall process or system being audited
C. Distinguish variations in a process over time
D. Determine process capability and uniformity
Correct answer: B
Explanation:
Flowcharts are one of the most powerful tools used by auditors to visually represent processes, procedures, and systems. These charts provide a step-by-step diagrammatic representation of how different components in a system or process interact, which is crucial in an audit environment. Let’s go through each option to explain why B is the correct answer.
A suggests that flowcharts can help analyze the causal factors of process dispersion. While flowcharts can depict the steps in a process and help to visualize how a system operates, they are not designed specifically to pinpoint causal factors of process dispersion. Dispersion generally refers to the spread or variability in process results, which would typically be more effectively analyzed using statistical tools or control charts, not flowcharts. While a flowchart might help understand the process itself, identifying dispersion would require different methods of analysis, such as regression analysis or statistical process control (SPC).
B is the correct answer because flowcharts are ideal tools for auditors to understand the overall process or system being audited. When auditing a process, an auditor needs a clear, visual representation of the system being assessed. Flowcharts map out the entire sequence of activities, decisions, inputs, and outputs within the process. This helps auditors identify any inefficiencies, bottlenecks, or risks in the workflow and facilitates their understanding of how the process should operate. It provides an at-a-glance view of how various parts of the system or process are interconnected and assists auditors in identifying areas for improvement or non-compliance with policies and procedures.
C states that flowcharts can help distinguish variations in a process over time. However, this function is typically handled more effectively by other tools, such as time series analysis, control charts, or run charts, which track changes over a given period. While a flowchart can help illustrate the general flow of a process, it does not inherently track the variation or changes in a process over time. For variation analysis, auditors would rely on data collection methods that measure performance across different periods.
D suggests that flowcharts are used to determine process capability and uniformity. Process capability refers to the ability of a process to produce outputs within specified limits, which is generally measured using specific statistical analysis techniques such as capability indices (Cp, Cpk). While flowcharts provide clarity on how a process works, they are not used to assess the capability or uniformity of that process, as this is outside the scope of what a flowchart represents. Instead, auditors would rely on tools such as statistical analysis, control charts, and performance metrics to evaluate these aspects.
In conclusion, B is the most accurate and relevant answer because flowcharts allow auditors to understand the overall process or system they are auditing by providing a clear, visual map of its components and steps. This helps auditors identify inefficiencies, gaps, or risks in the system, which is central to the auditing process. Flowcharts are primarily a diagnostic and visual tool for understanding process flow, making them essential for providing insight into the operation of the system being examined.
Question No 9:
An auditee responds to a corrective action request by stating that the problem has never occurred before and is "not the norm for our operation."
Which of the following is the most appropriate action for the lead auditor?
A. Note that the deficiency is the result of a random occurrence.
B. Draft a response explicitly requesting a more concise root-cause analysis.
C. Confer with the audit client to assess the appropriateness of the response.
D. Schedule a follow-up audit immediately.
Correct answer: B
Explanation:
In auditing, when an auditee responds to a corrective action request by stating that a problem has "never occurred before" or is "not the norm," it’s important for the lead auditor to critically assess this response. This kind of statement typically signals a lack of thorough investigation into the root causes of the issue or a possible underestimation of the problem’s significance. The lead auditor’s role is to ensure that the auditee takes appropriate and effective corrective actions to prevent recurrence of the issue. Therefore, the correct action is to request a more concise root-cause analysis.
Option B is the best response because it addresses the need for a clear and thorough analysis of why the problem occurred, even if it is perceived as an isolated or uncommon event. The lead auditor must ensure that the auditee is not simply dismissing the issue as an anomaly but is instead engaging in a meaningful examination of its potential causes. Without understanding the root cause, corrective actions might be ineffective or incomplete. The auditee must demonstrate that the corrective actions will address the underlying causes of the problem, not just treat the symptoms.
Option A is inappropriate because it suggests accepting the deficiency as a random occurrence, which would undermine the purpose of corrective actions. Even if the problem seems rare, it is crucial to investigate whether systemic issues contributed to its occurrence. Auditors should not accept "random occurrence" as an excuse for non-compliance or failure to meet standards.
Option C is not as effective as option B. While conferring with the audit client could be part of the process, simply assessing the appropriateness of the response does not directly lead to the needed corrective action. The lead auditor needs to be more proactive in requesting a deeper analysis and clarification from the auditee, which would be captured by asking for a more detailed root-cause analysis.
Option D suggests scheduling a follow-up audit immediately, which might not be necessary if the auditee can provide an adequate and actionable corrective action plan. Follow-up audits are typically scheduled after corrective actions have been implemented, and the auditor needs to ensure that the auditee understands the root causes before taking corrective actions.
In conclusion, the most appropriate action is for the lead auditor to request a more concise root-cause analysis to ensure that the auditee investigates the issue thoroughly and implements corrective actions that address the actual causes of the problem. This helps maintain the integrity of the audit process and ensures compliance in the long term. Thus, B is the correct choice.
Question No 10:
What is a technique used in audit reporting to prioritize audit findings?
A. Weibull distribution
B. Risk-benefit ratio
C. Cognitive dissonance
D. Ishikawa diagram
Correct Answer: B
Explanation:
In the context of audit reporting, it is crucial to identify which audit findings need to be addressed first and most urgently. Prioritizing findings ensures that resources are allocated efficiently, and critical issues are resolved before they can lead to more significant problems. The risk-benefit ratio is a commonly used technique to prioritize audit findings because it helps auditors assess which issues present the highest potential risk and the most substantial benefits if addressed.
Let’s break down each option to understand why B is the correct answer:
Weibull distribution (A):
The Weibull distribution is a statistical tool used primarily to model reliability and failure rates over time. While it is useful in the field of engineering and reliability analysis, it is not typically associated with prioritizing audit findings. The Weibull distribution can help model the likelihood of failure or defects but does not directly prioritize or categorize audit issues in a way that would be applicable for addressing findings.
Risk-benefit ratio (B):
The risk-benefit ratio is a decision-making tool that compares the potential risks of a particular finding with the benefits of addressing that issue. In an audit context, this means evaluating how critical a finding is based on its risk (e.g., the potential harm it could cause if ignored) versus the benefit (e.g., the improvement or risk mitigation that would come from resolving it). A high-risk, high-benefit finding would typically be prioritized over low-risk, low-benefit findings. This technique is directly relevant to audit reporting and is commonly used in various fields to prioritize actions effectively.
Cognitive dissonance (C):
Cognitive dissonance refers to the mental discomfort experienced when one’s beliefs are contradicted by new information. While it is a valuable concept in psychology and behavioral science, it is not used as a method for prioritizing audit findings. Cognitive dissonance could be relevant in understanding how individuals react to audit findings, but it does not function as a technique for systematically ranking or prioritizing audit issues.
Ishikawa diagram (D):
The Ishikawa diagram (also known as a fishbone diagram) is a visual tool used to identify the root causes of problems. It is particularly useful for cause-and-effect analysis, helping teams trace issues back to their origins. However, the Ishikawa diagram is not specifically designed to prioritize findings; rather, it helps in identifying and analyzing the causes of a particular issue. While the Ishikawa diagram is a valuable tool for audits, its purpose is not to prioritize findings but to uncover underlying causes.
Risk-benefit ratio (B) is the technique that directly addresses how to prioritize findings based on an assessment of the potential risks associated with each finding and the benefits of addressing them. Auditors can use this tool to make informed decisions about where to focus their efforts and resources. For example, findings that could lead to significant financial or legal consequences should be prioritized over minor inefficiencies. This approach ensures that critical issues are addressed promptly to minimize the overall risk to the organization.
Top Training Courses
SPECIAL OFFER: GET 10% OFF
This is ONE TIME OFFER
A confirmation link will be sent to this email address to verify your login. *We value your privacy. We will not rent or sell your email address.
Download Free Demo of VCE Exam Simulator
Experience Avanset VCE Exam Simulator for yourself.
Simply submit your e-mail address below to get started with our interactive software demo of your free trial.